Wire eroding systematically
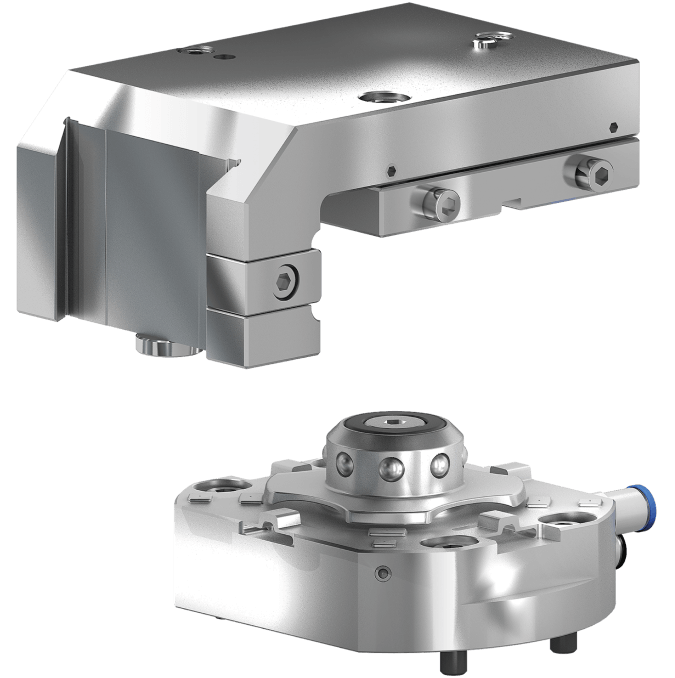
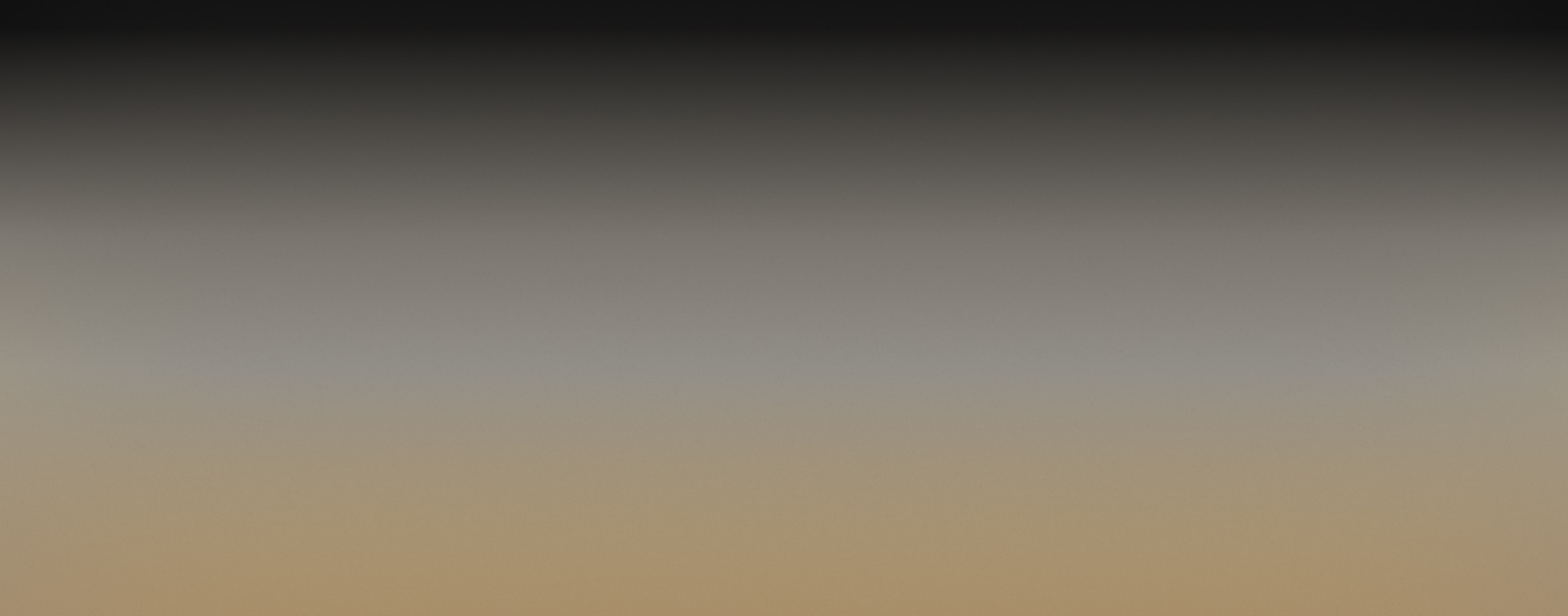
Precision clamping with SMART GRIP – the zero-point palletizing system for wire EDM-ing.
1. SMART GRIP EASY
SMART GRIP EASY offers you a simple, costeffective entry into economical and processreliable clamping technology. The fixtures, clamping devices and workpieces can be clamped and aligned in the machine. The system can be upgraded to the SMART GRIP AIR zero-point clamping system at any time.
2. SMART GRIP AIR
SMART GRIP AIR is the zero-point clamping system. This allows the aligning and clamping of fixtures and workpieces outside the machine. With SMART GRIP AIR, the workpieces can be placed in the machine fully automatically with a robot. Productivity is significantly increased by SMART GRIP.
3. SMART GRIP BAR
SMART GRIP BAR is the optimum solution for large workpieces to be clamped directely in the machine. The calmping bars also allow multiple clamping of different or identical workpieces with optimum utilisation of the machine‘s entire travel range.
Up to 45% more efficiency
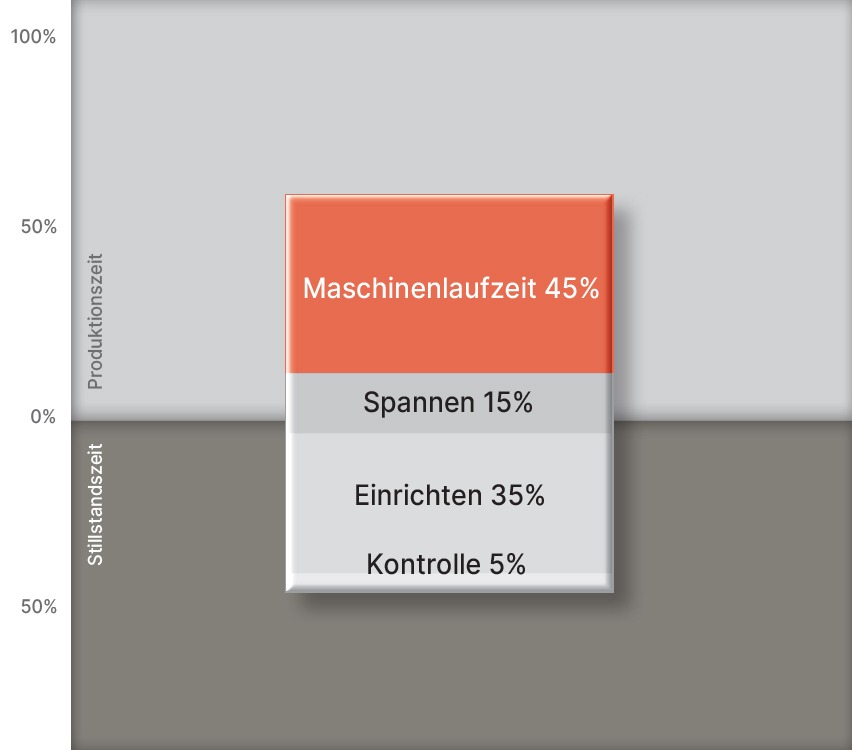
Time-consuming set-up in the machines
- Uneconomic manufacturing
- Non-optimized manufacturing processes
- No standardization
- High costs per unit
- Excessive delivery times
- Unfulfilled delivery dates
- High error rate
- Pricing pressure and competitive pressure
- High risk of collision
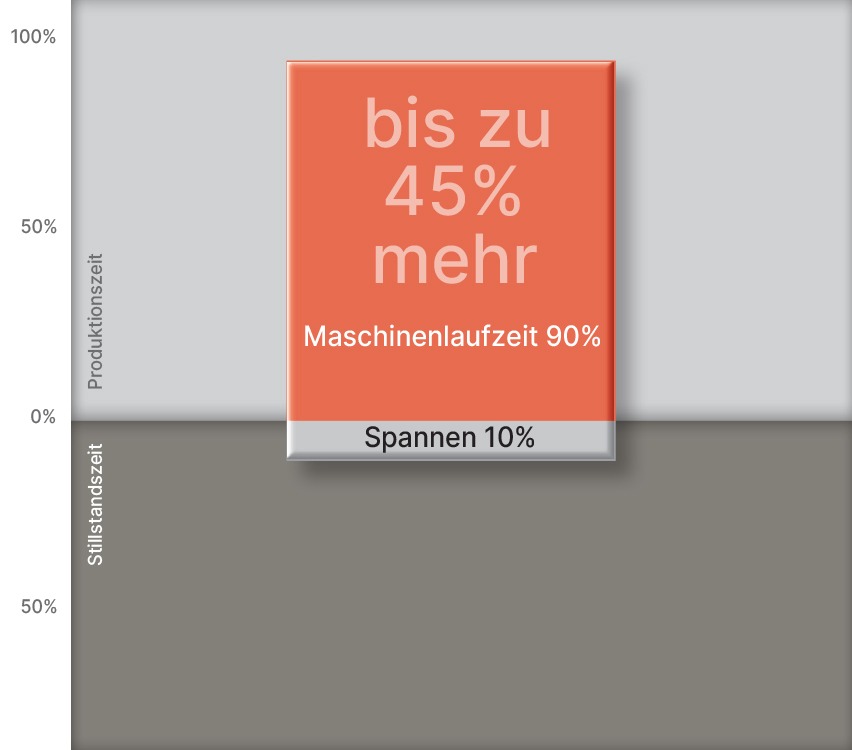
Main time-parallel set-up outside the machines.
- Higher productivity and income
- Optimized manufacturing processes
- Standardized interfaces
- Low unit costs
- Reduced delivery times
- Adherence to delivery dates
- Low error rate
- Competitive capacity
- Collision-free clamping thanks to presetting
9 Advantages at a glance
Technology
High quality through and through.
Granting process safety whilst clamping with power and precision.
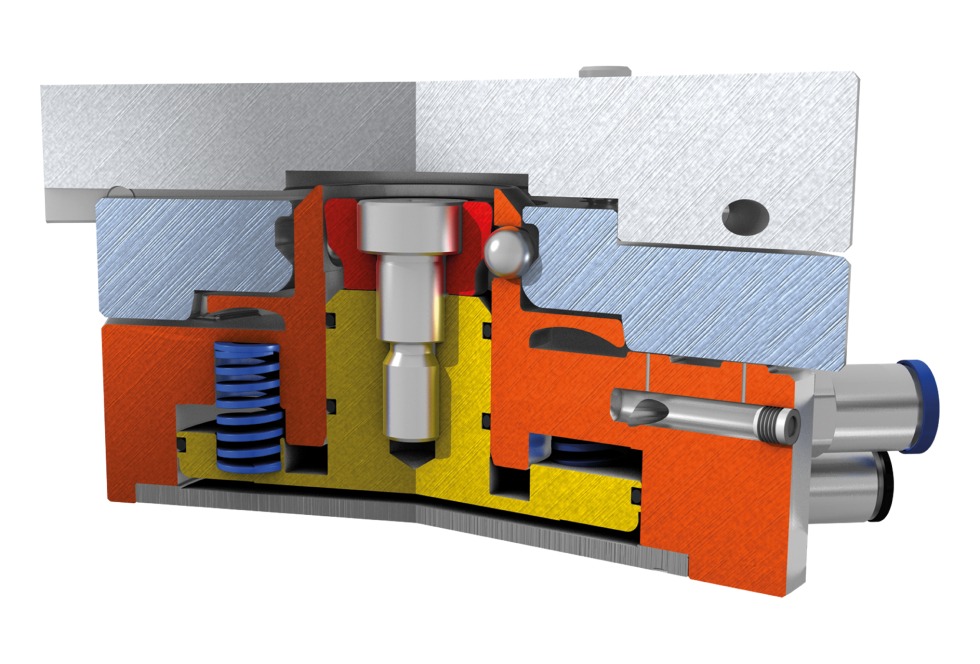
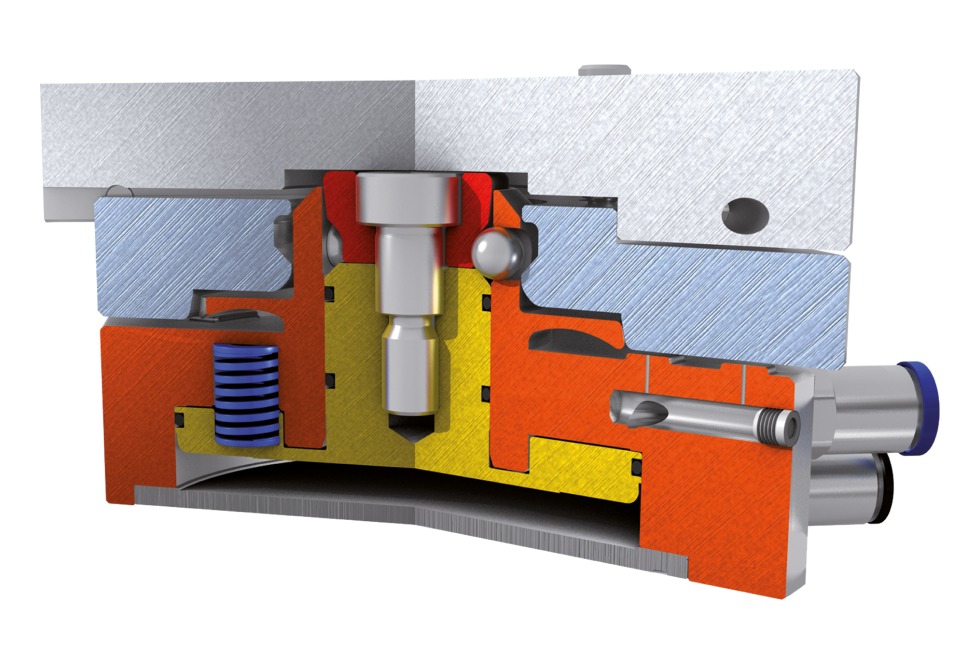
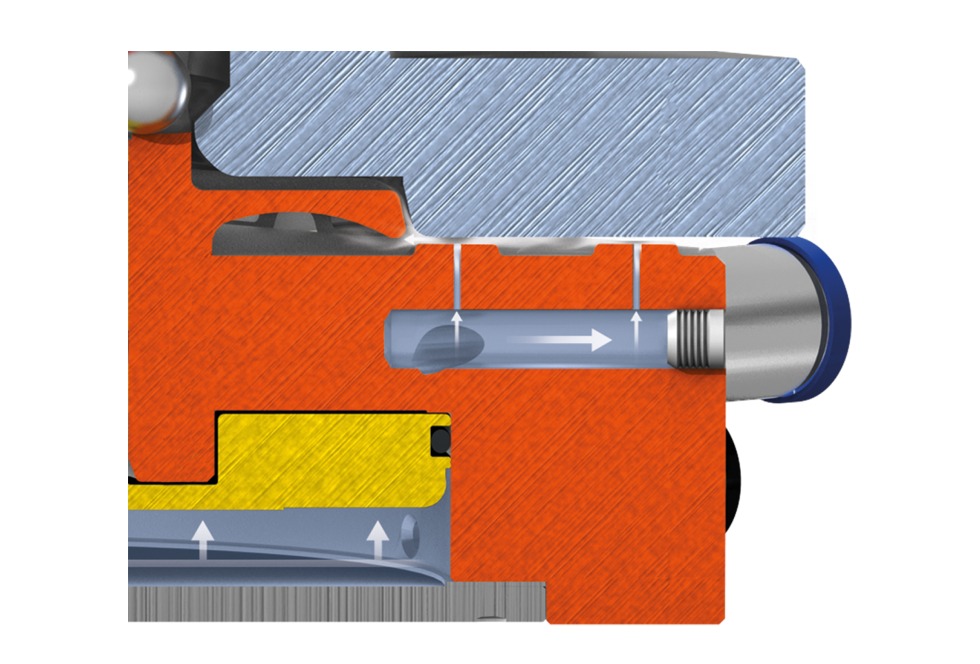
Unlocked SMART GRIP
In a released state, a continuous flow of air effectively cleans and protects the Z-references from dirt and contamination. This airflow ensures that any debris or particles are blown away, maintaining the cleanliness and integrity of the reference surfaces. As a result, the system remains in optimal condition, contributing to its overall performance and reliability.
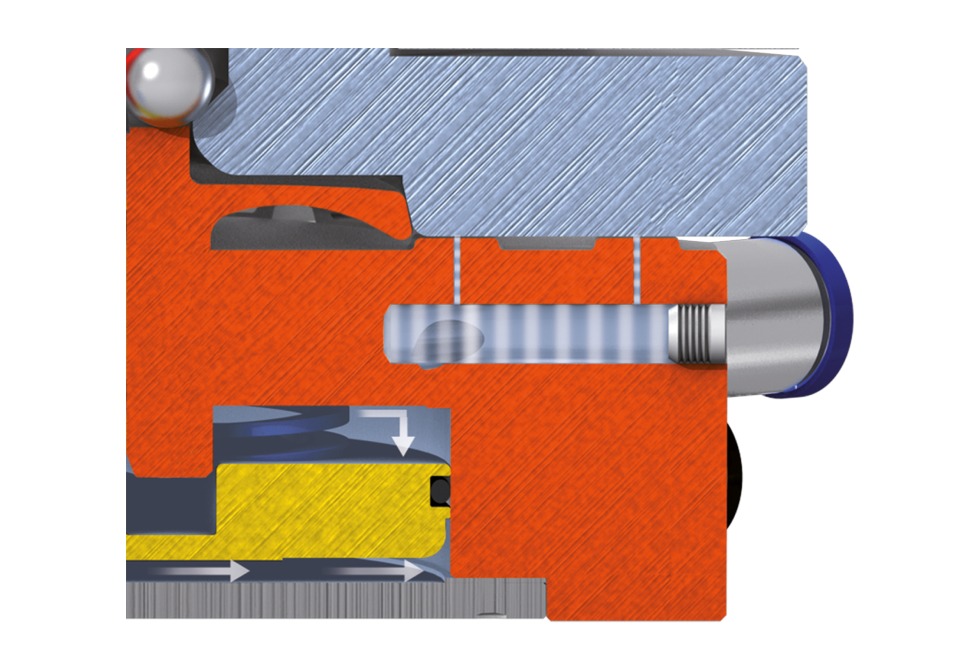
Locked SMART GRIP
In a locked state, the airflow accumulates, causing the pressure to rise, signaling to the system that the pallet is securely clamped in place. This interruption indicates that the clamping process has been successfully completed, allowing production to commence. With the pallet firmly held, all machining operations can begin safely and efficiently, ensuring that the workpiece remains stable and accurately positioned throughout the manufacturing process.
Loading
With SMART GRIP AIR you choose double integrated safety.
Pre-centering and loading
Classic clamping systems
SMART GRIP AIR
Maintenance
Maintenance with minimum effort.
In contrast to other palletizing systems, all important wear parts of the SMART GRIP system are accessible from the outside. The system is easy to clean. Complete disassembly is unnecessary. The zero point is not lost. This process only requires little time. With SMART GRIP, there is no risk of idle time due to dirt or abrasive wear. The external clamping mechanism is freely accessible and can easily be cleaned by yourself at any time.
Benefit from:
- Low time and costs for cleaning
- Maintenance „without zero-point loss”
- Highest process reliability
- Maintenance within very short time
- Maintenance „inhouse” by your own machine user without expensive service technician

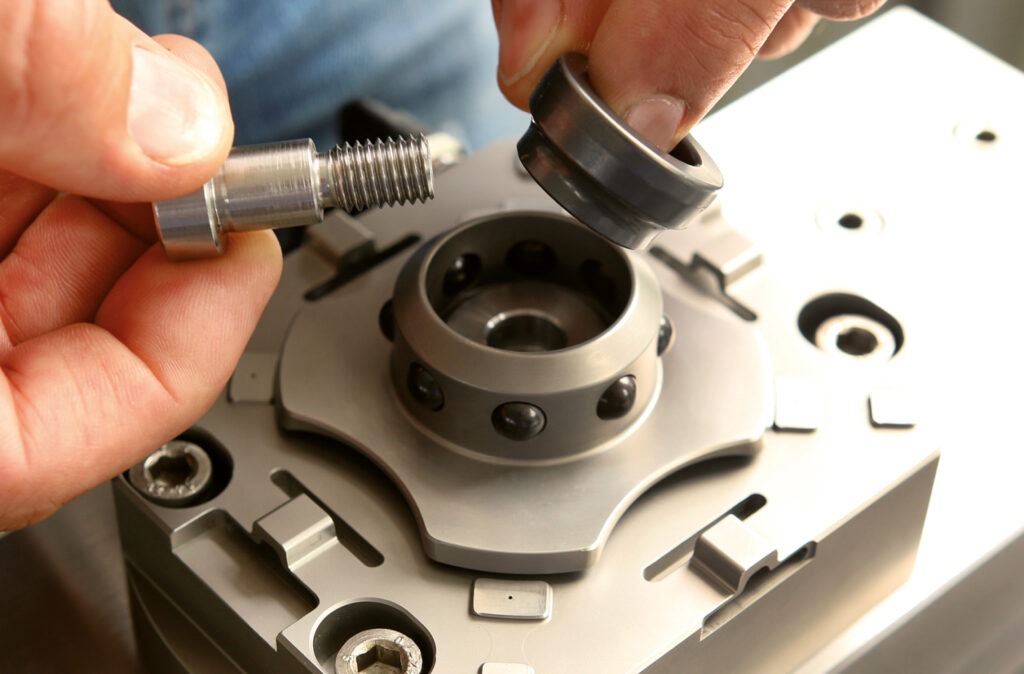
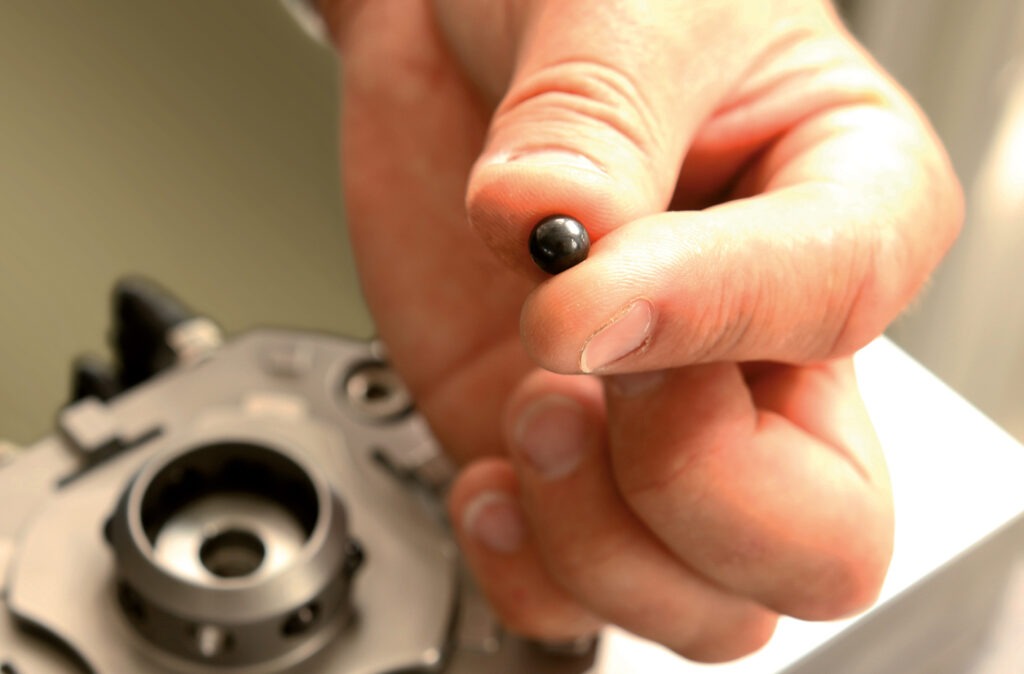
Accuracy
Accurately repeatable.
System accuracy.
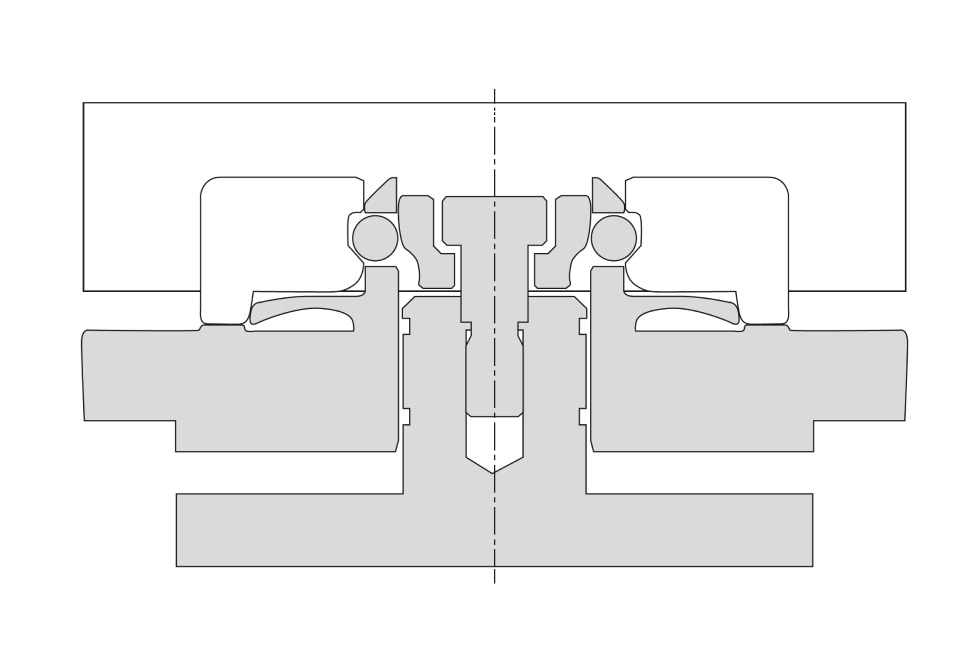
Your technical advantages:
- Cone-shaped, spring-loaded alignment with planar support (HSK principle, hollow pole cone)
- Four axial centering spring lugs guarantee tolerance-free centering
- Index cams for exact positioning
Z-References
SMART GRIP AIR is always equipped with a Z-reference cleaning system. Z-reference surfaces are cleaned at every chucking process. This is important for high levels of accuracy, process safety and lifespan. The hardened and rust-proof SMART GRIP AIR reference surfaces, both in the palletizing system and the pallets, make this system virtually non-wearing and readily automatable. Look forward to a long lifespan and consistent precision of the system.
Your technical advantages:
- Automatic Z-reference cleaning
- System control for automation possible at any time
- Overpressure against the penetration of erosion particles or dielectric fluid
- Consistently high process reliability
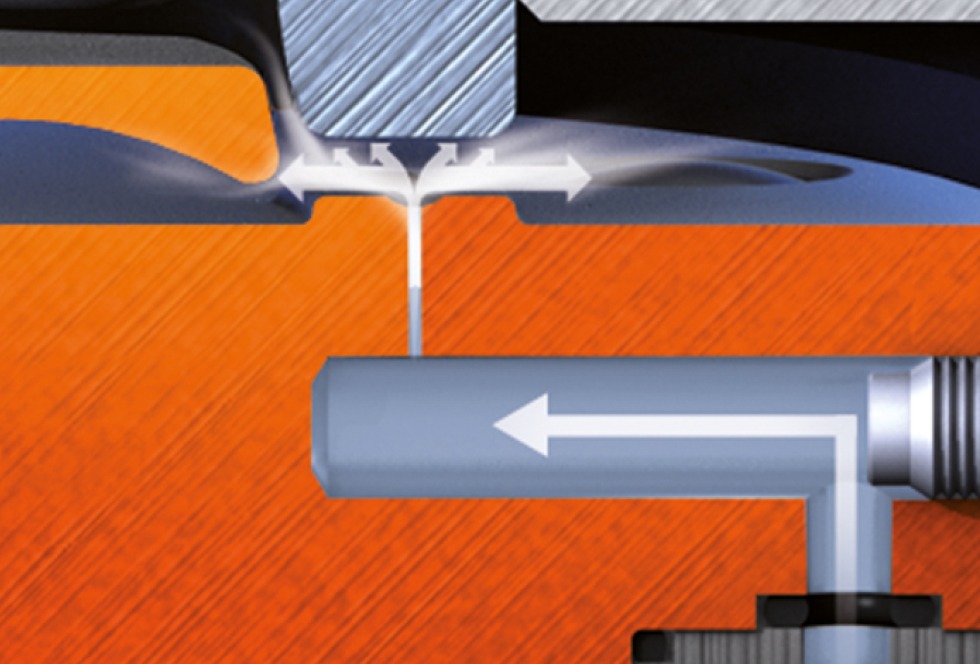
In a released state, a continuous flow of air serves to clean and protect the Z-references from dirt and contamination. This ongoing airflow helps to effectively blow away any debris or particles, ensuring that the reference surfaces remain clean and in optimal condition. By preventing the accumulation of dirt, the system maintains its reliability and precision, which is essential for high-quality machining operations.
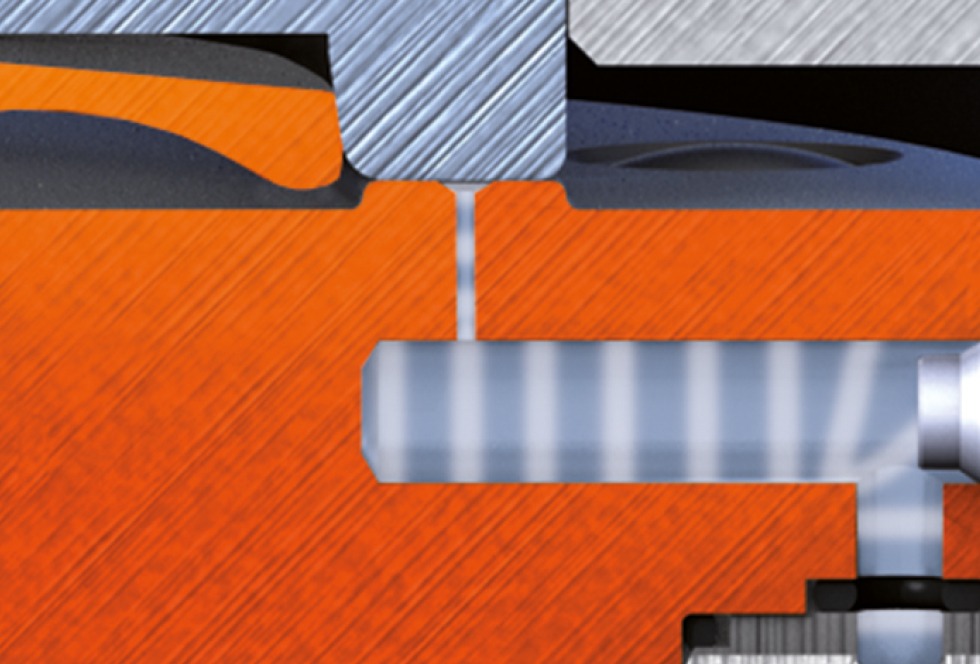
In a locked state, the airflow is interrupted, serving as a signal to the system that the pallet is securely clamped in position. This interruption confirms that the clamping process has been successfully completed, allowing production to commence. With the pallet firmly secured, all machining operations can proceed safely and efficiently, ensuring that the workpiece remains stable and accurately positioned throughout the entire production process.
Process safety
By means of hardened, rust-proof reference surfaces, both on the pallet and the pallet carrier, as well as by the additional possibility of monitoring by Z-reference feedback, SMART GRIP can be automated at any time. SMART GRIP AIR pallet carriers always offer the possibility of system control via the Z-references.
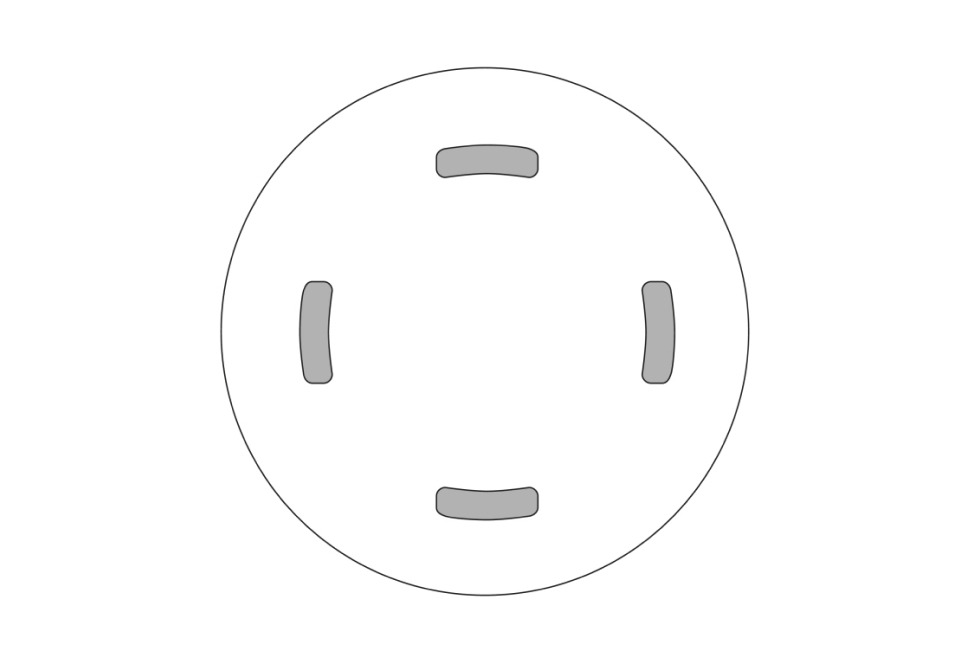
Profit from:
- the possibility of automation
- at any time
- without additional costs
- with existing SMART GRIP pallet
Material, Lifespan, Clamping force
SMART GRIP AIR is made of high quality materials. The pallet carriers chuck selflocking with a clamping force of 15.000 N. Even under high pressure, e.g. under high machining forces or during a machine crash, pallets cannot be ripped from the palletizing system. The SMART GRIP AIR pallet carriers as well as the pallets, clamping devices and adapters are corrosion-restistant.
Result:
- higher accuracy
- higher lifespan
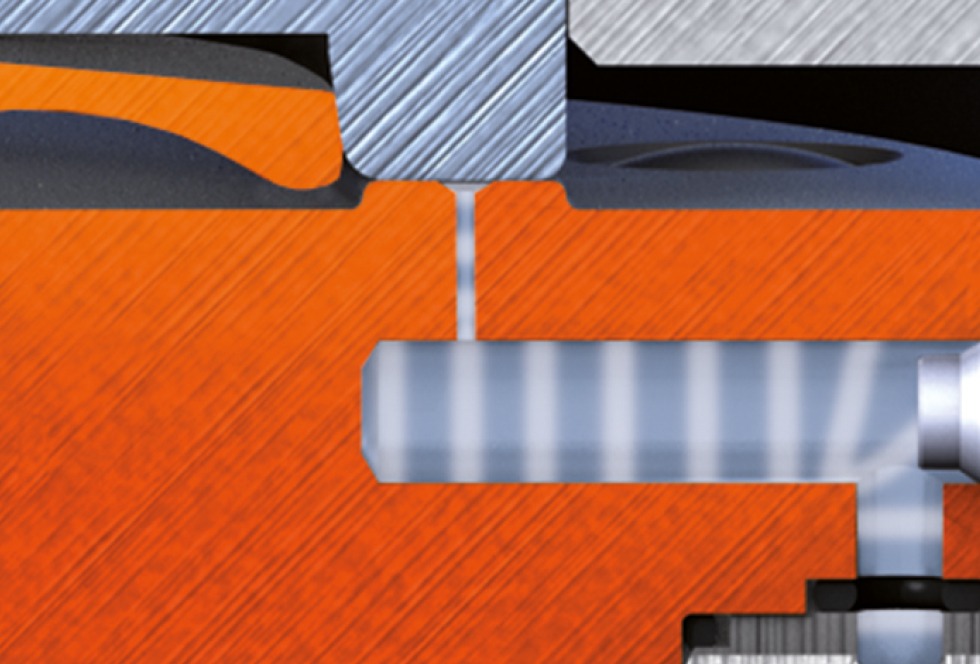
In a locked state, the airflow is interrupted, serving as a signal to the system that the pallet is securely clamped in position. This interruption confirms that the clamping process has been successfully completed, allowing production to commence. With the pallet firmly secured, all machining operations can proceed safely and efficiently, ensuring that the workpiece remains stable and accurately positioned throughout the entire production process.
Investment and gain
(palletized >35% potential extra operating time)
acquisition costs of your machine tool
Basic equipment ~ 15.000.- € and automation
Sum
[= total investment divided by 6]
[= (total investment x 4.5 %)÷2 ]
regarding occupancy cost of machine space
Maintenence costs
General share of wages
Sum of positions
Fixed costs/year divided by total runtime
(Ex. A: 80% , Ex. B: 65%, Ex. C: 50% of the wages / total runtime)
estimated share of expendable goods/hr.
estimated share of energy/hr.
costs Estimated share of varaible costs
Sum of positions
Fixed costs/hr. + variable costs/hr.
Hourly rate attainable on the market
attainable hourly rate/hr. minus production costs/hr.
difference derived from prod. costs and attainable hourly rate multiplied by total runtime
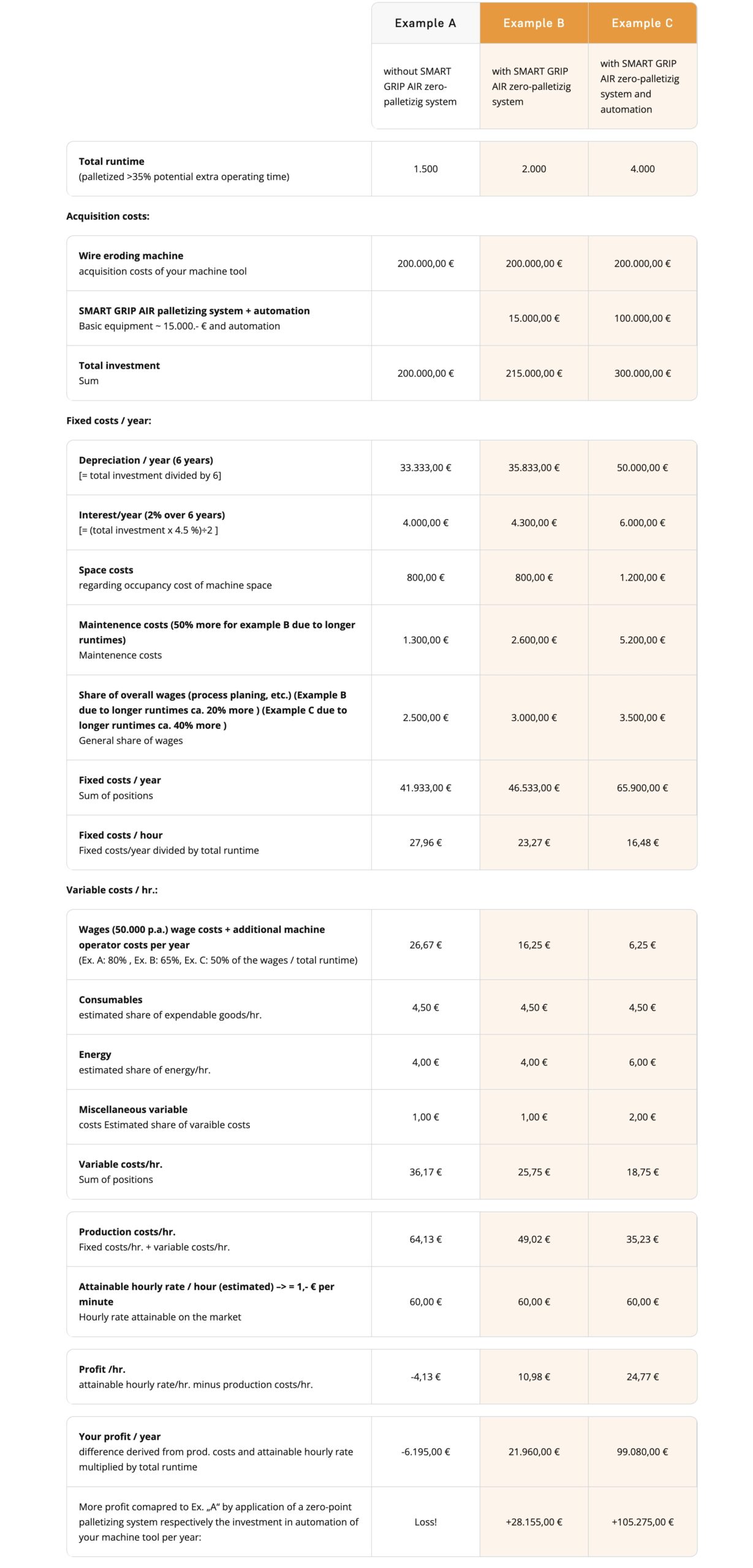
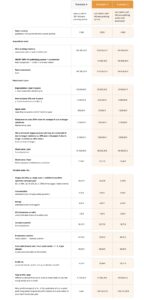
Application examples
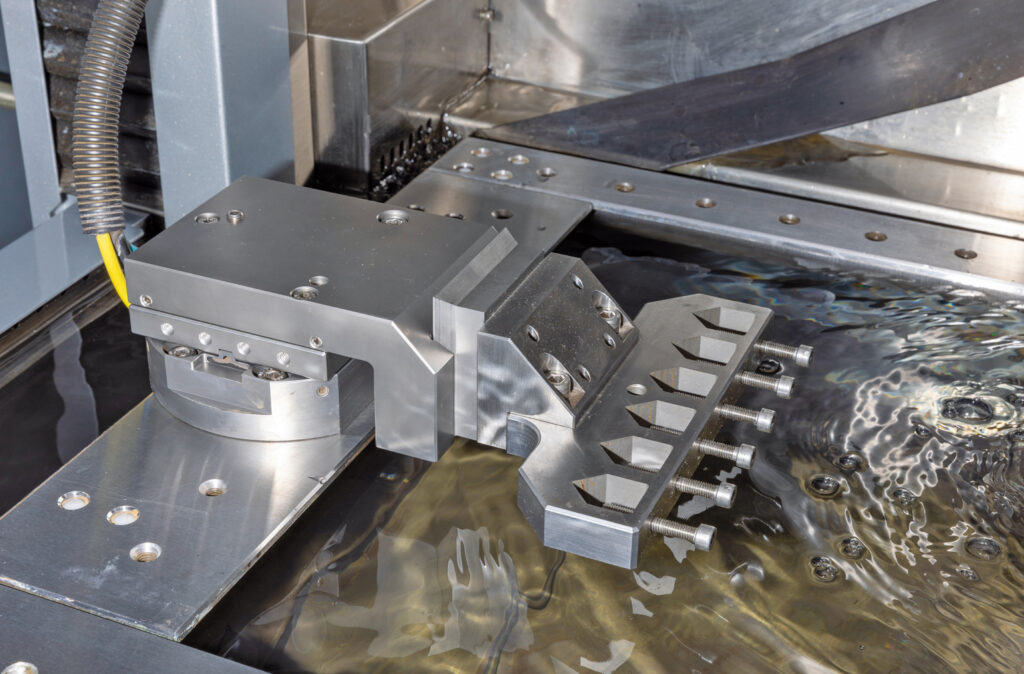
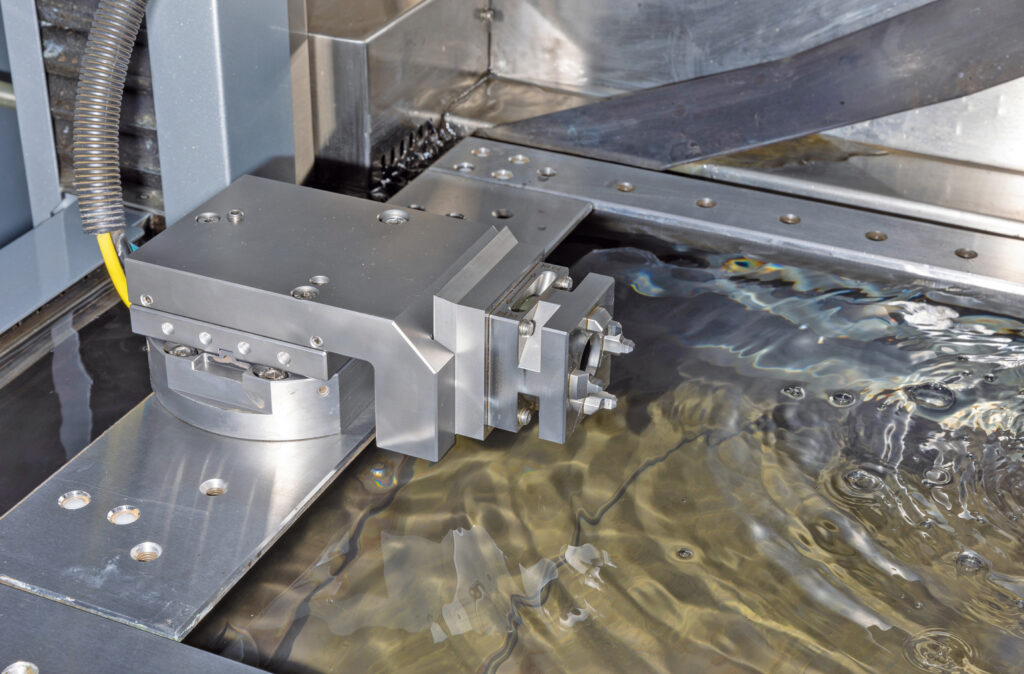
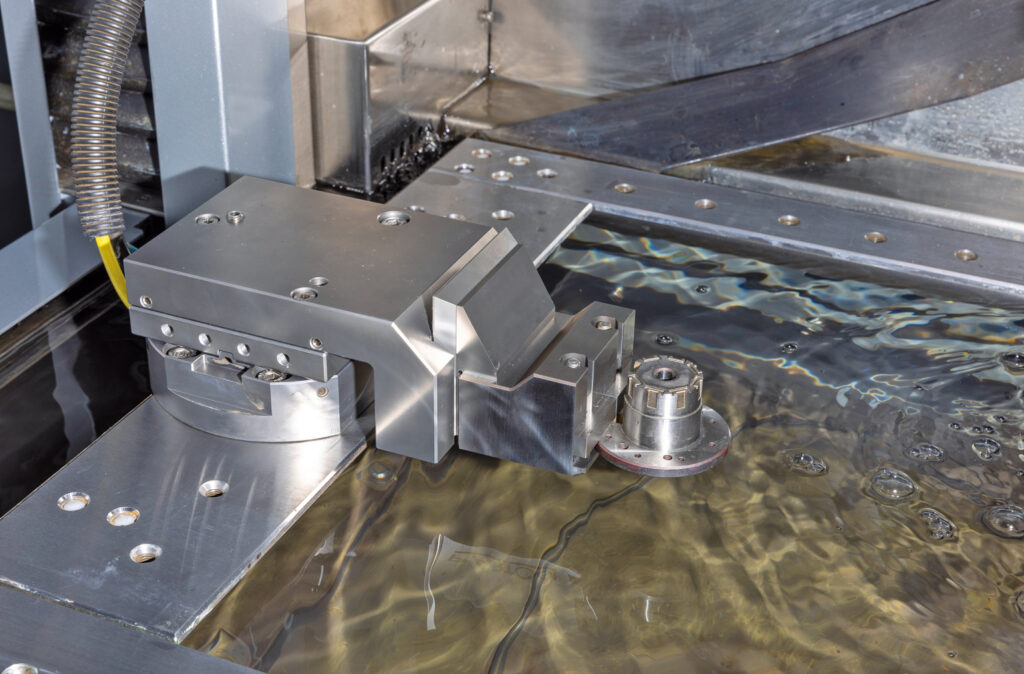
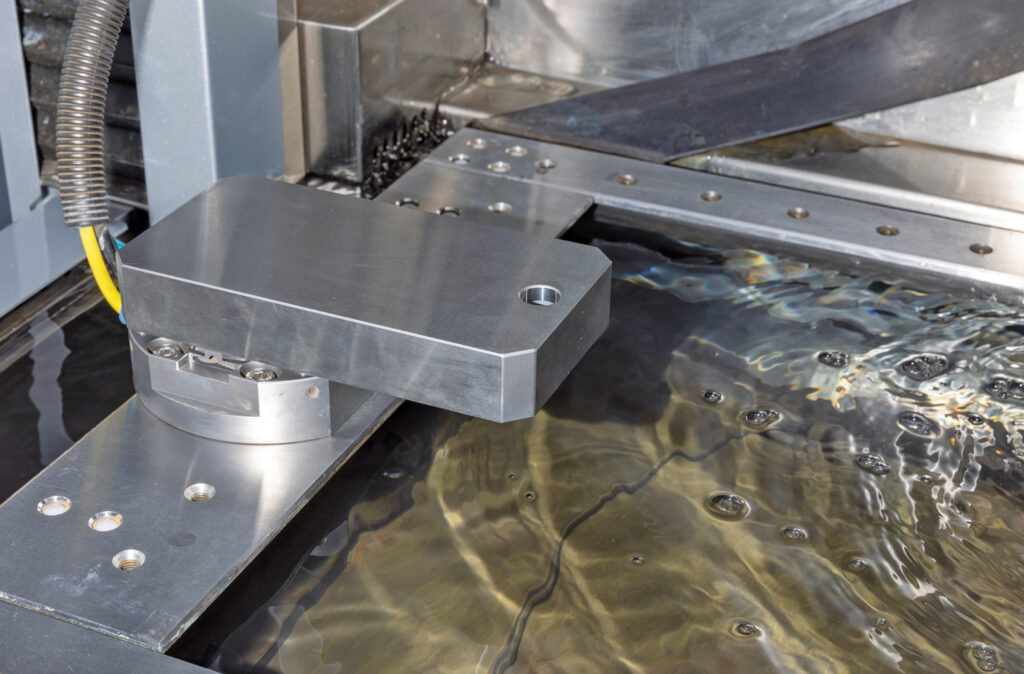
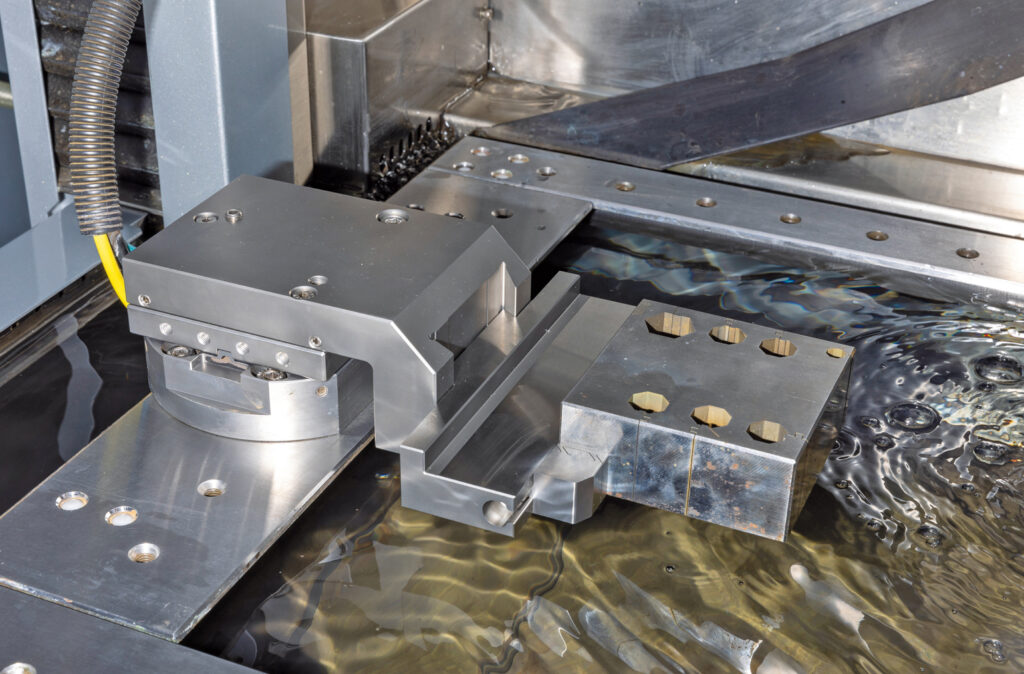
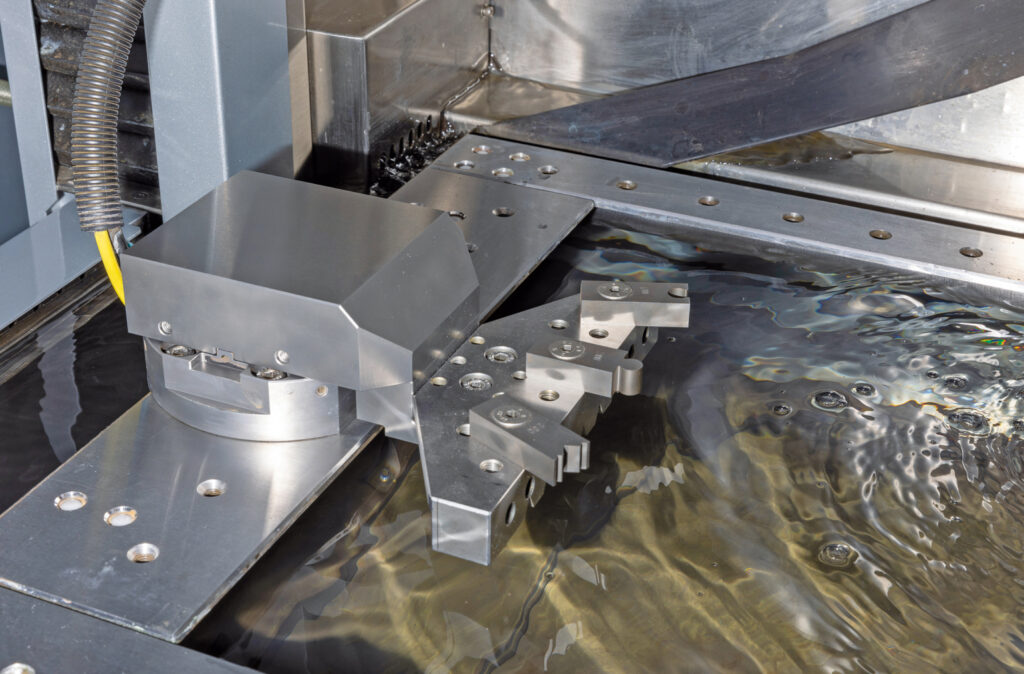
Download Brochure
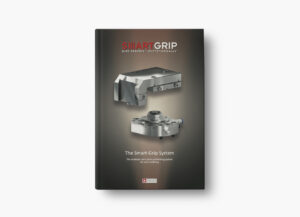