Clamping Systematically
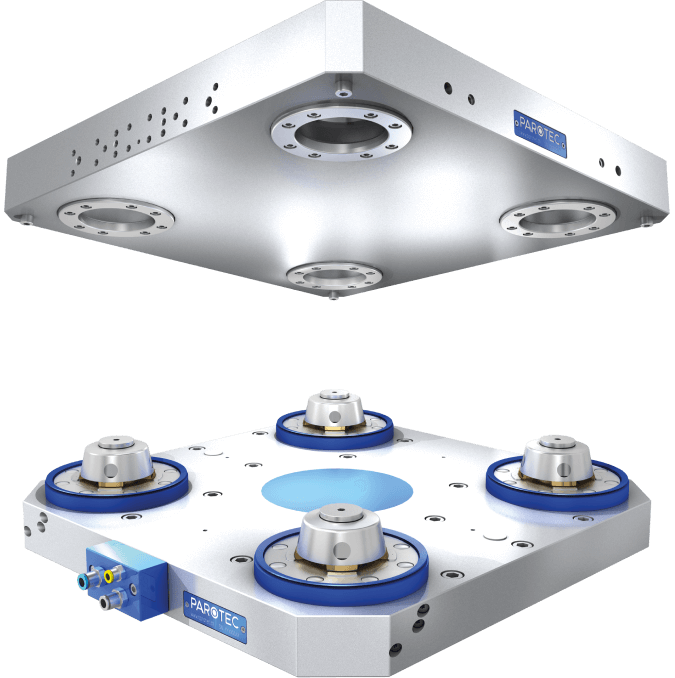
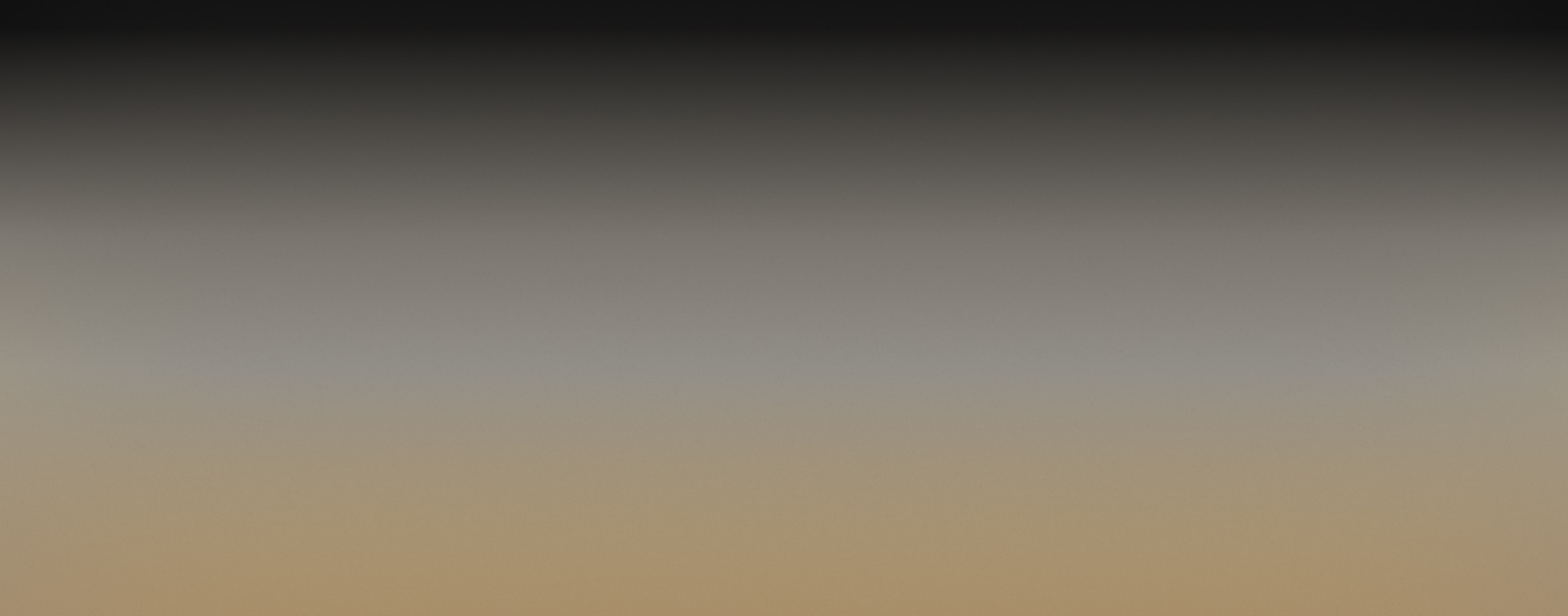
The consistant zero point clamping system for the heavy weight classes.
What is a zero point palletizing system?
A zero point palletizing system allows you to clamp and position work pieces, clamping media and fixtures quickly and precisely. The standardised interfaces drastically reduce set-up time, particularly for single workpieces and small batch production, thereby increasing effective machine uptime and productivity.
Up to 45% more efficiency
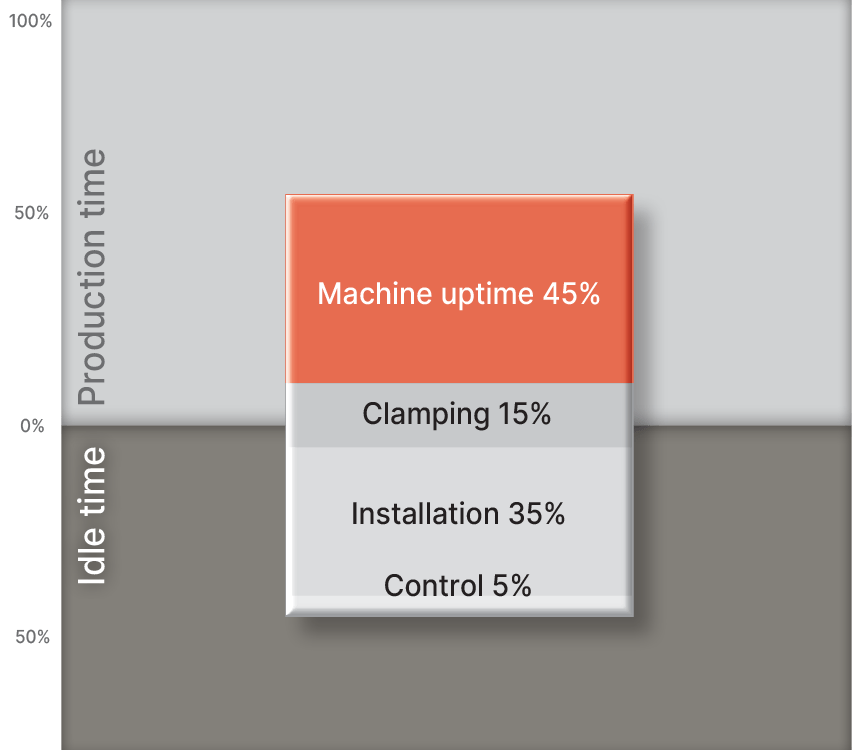
- Uneconomical production
- Non-optimized manufacturing processes
- Lack of standardization
- High unit costs
- Excessive lead times
- Missed delivery deadlines
- High error rate
- Price and competitive pressure
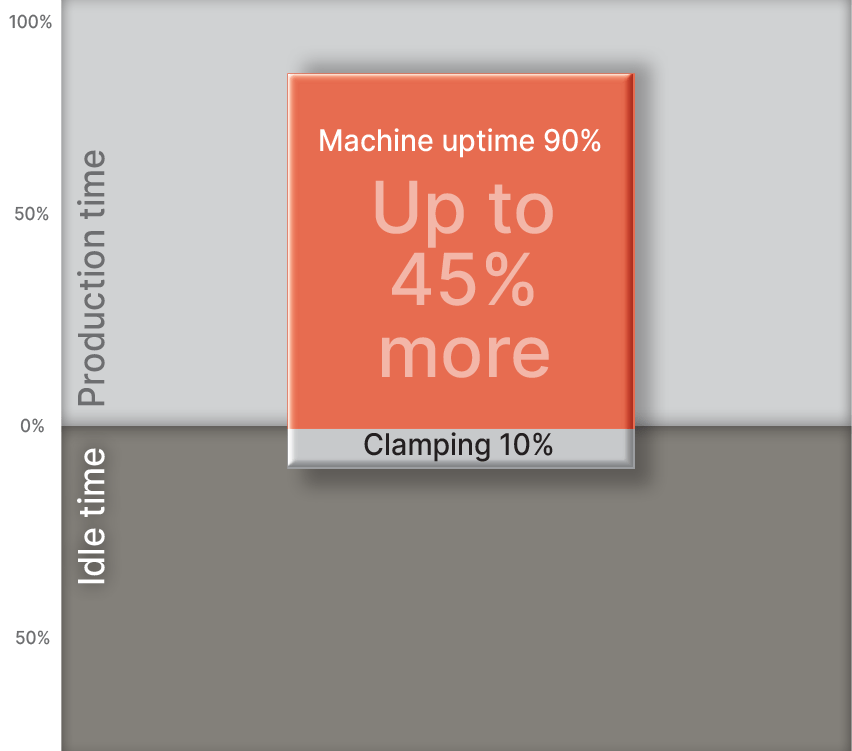
- Higher productivity and yield
- Optimized manufacturing processes
- Standardized interfaces
- Low unit costs
- Shorter lead times
- On-time delivery
- Low error rate
- Competitiveness
10 Advantages at a Glance
The system
Disadvantage of classic clamping systems
Advantage of GENIUS GRIP
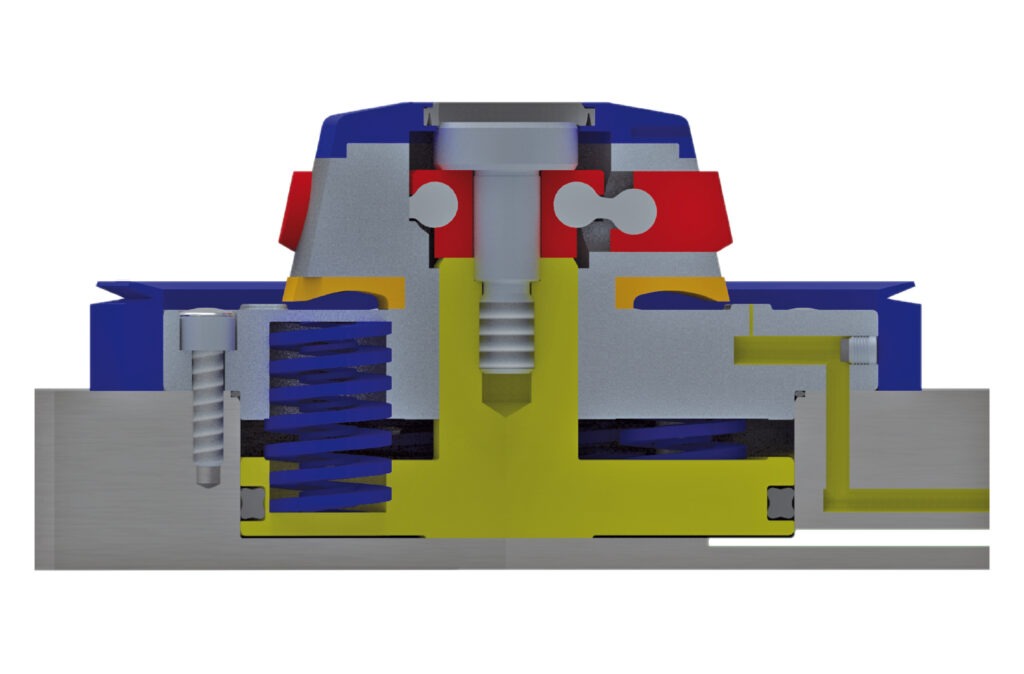
Centering unit
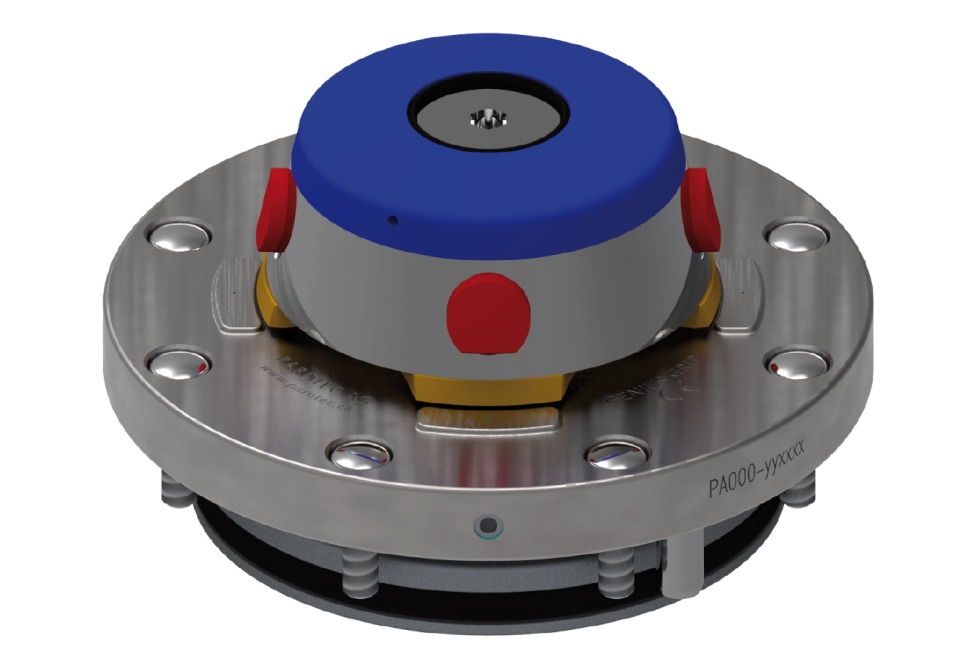
Centering unit
The centering unit features an axial spring centering mechanism, which ensures precise alignment of the workpiece, along with a face support that provides additional stability during the clamping process. This unit also includes a Z-reference cleaning function, which helps maintain the cleanliness and integrity of the reference surfaces, ensuring optimal performance and accuracy during machining operations.
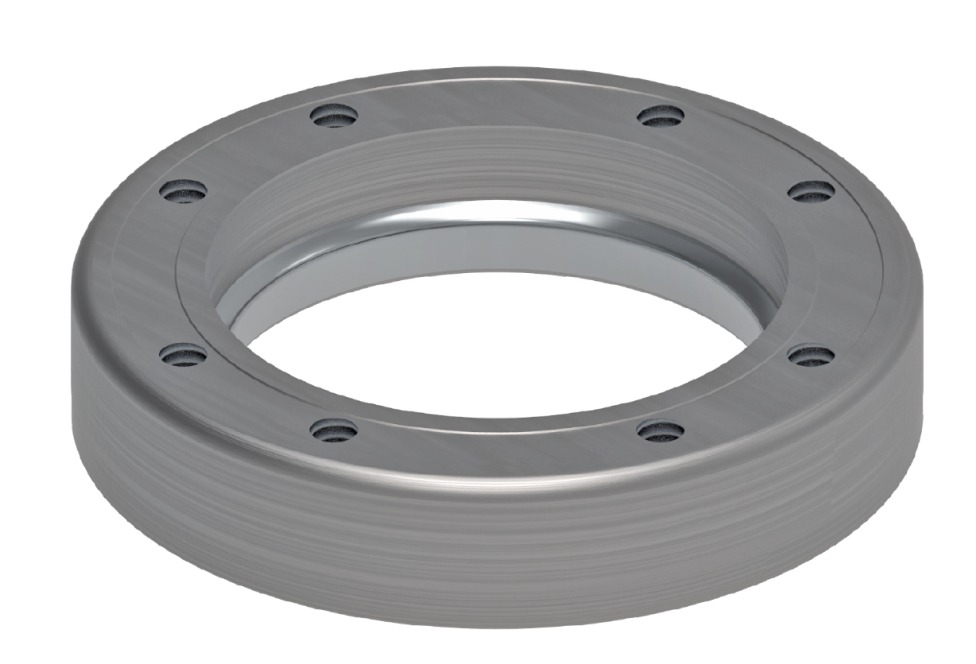
Centering clamping sleeve
The GENIUS GRIP centering and clamping sleeves are designed to be hardened and corrosion-resistant, ensuring durability and longevity in various working environments. This construction helps maintain their performance over time, even in challenging conditions, providing reliable clamping and centering solutions for precision machining tasks.
The System
With GENIUS GRIP you choose doubly integrated safety.
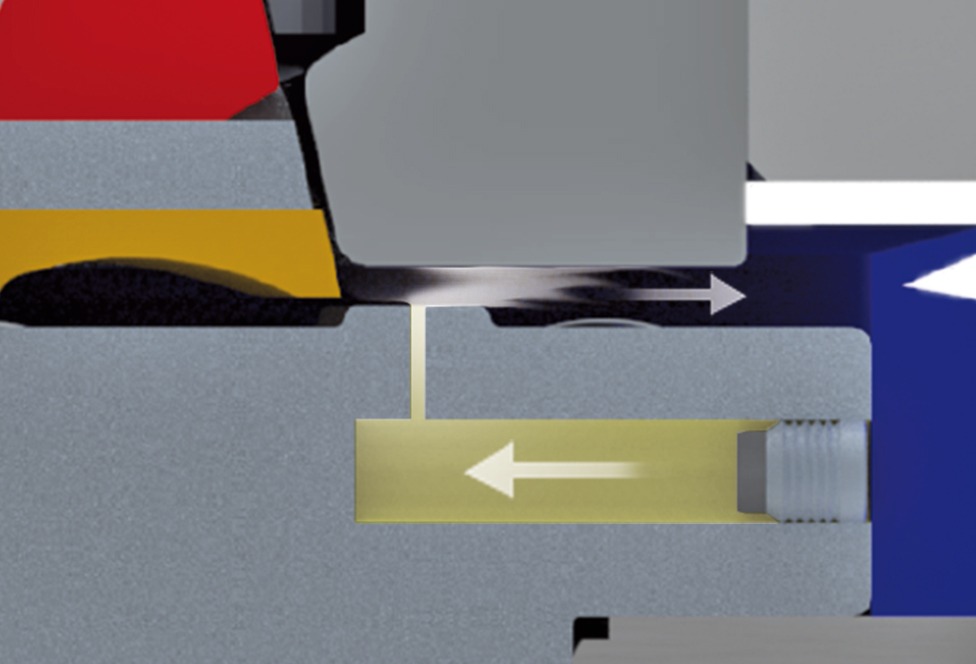

Loading
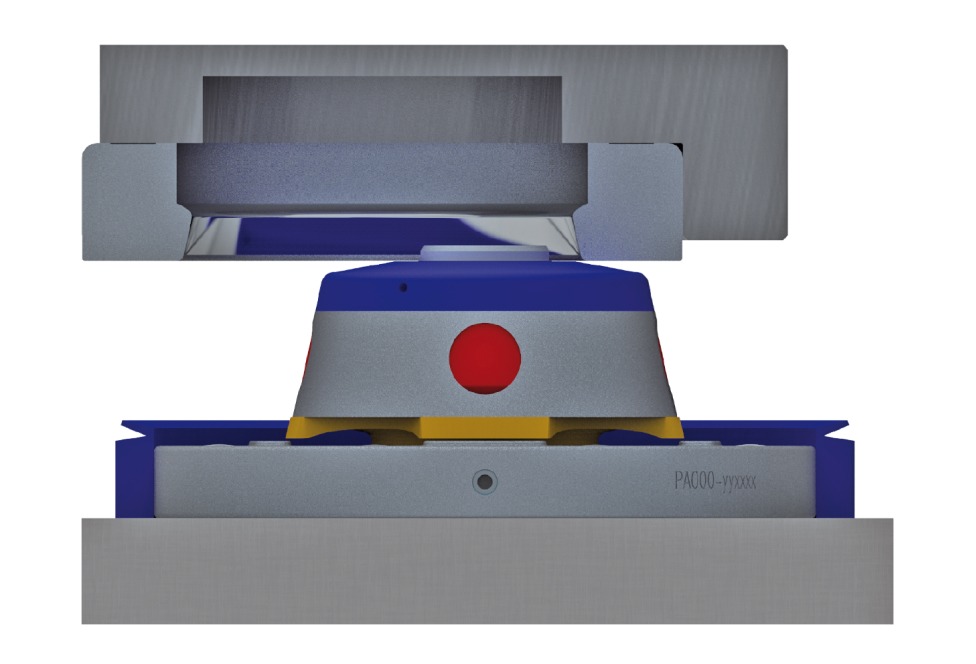
Large lateral offset? No problem! This means that the system can easily accommodate significant side adjustments without compromising accuracy or stability. Whether you’re working with various workpieces or adjusting setups for different machining tasks, the design ensures that you can achieve the necessary alignment without any issues. This flexibility enhances operational efficiency and allows for seamless transitions between different jobs.
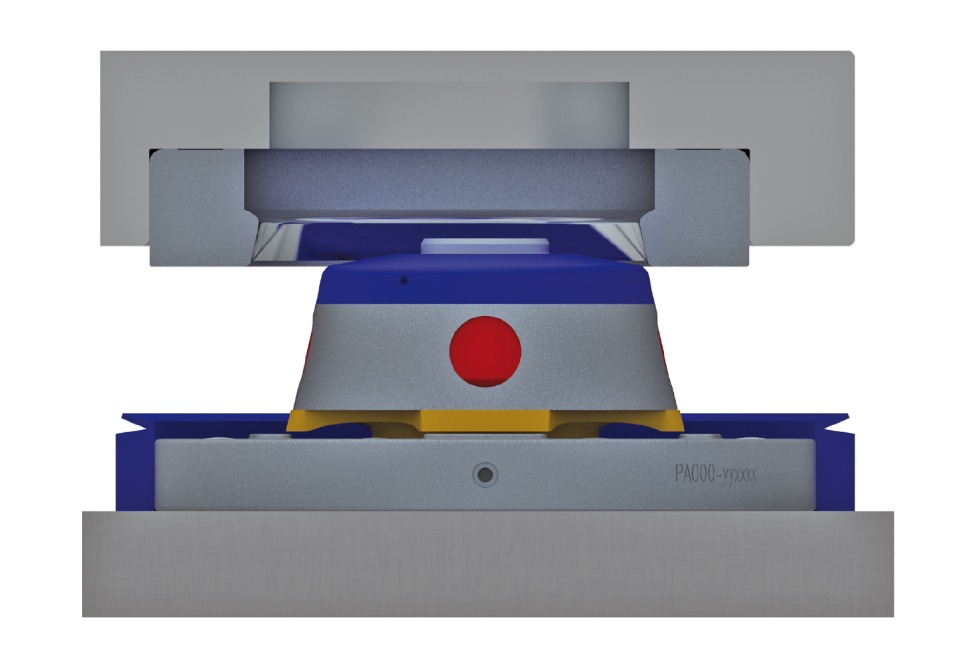
With the large pre-centering feature, the pallet always finds its correct position effortlessly! This design ensures that the pallet aligns accurately each time it is loaded, reducing setup time and enhancing overall efficiency. The reliable pre-centering mechanism contributes to precise clamping and machining operations, allowing for consistent performance and minimizing the risk of errors during production.
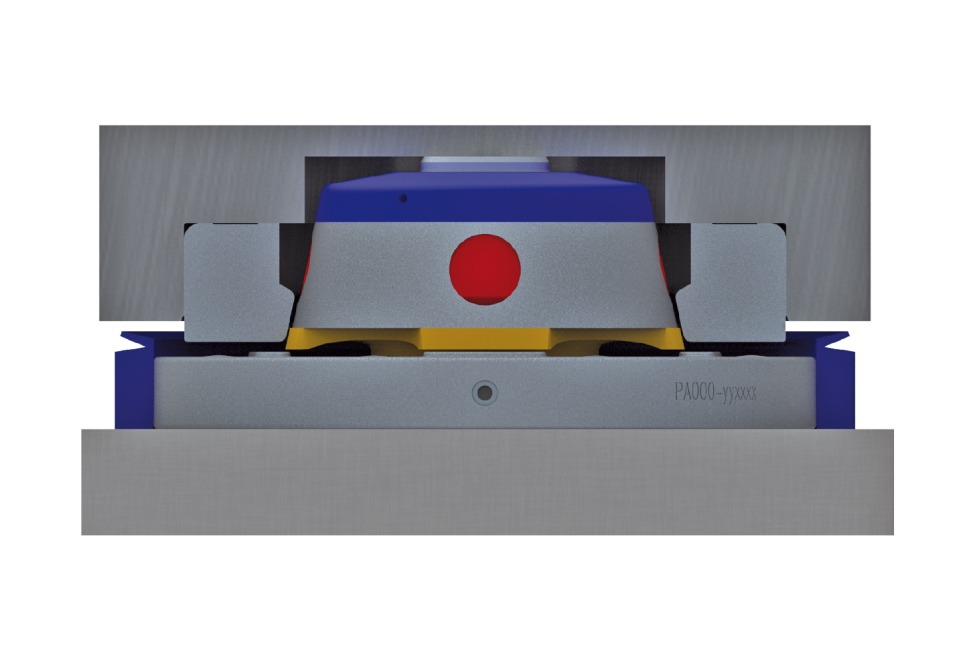
When loosened, the pallets are elevated by 2.2 mm. This lift ensures that the reference surfaces do not make contact until the clamping process begins, preventing any potential damage and allowing for precise alignment during setup. This feature enhances operational efficiency and maintains the integrity of the workpieces throughout the machining process.
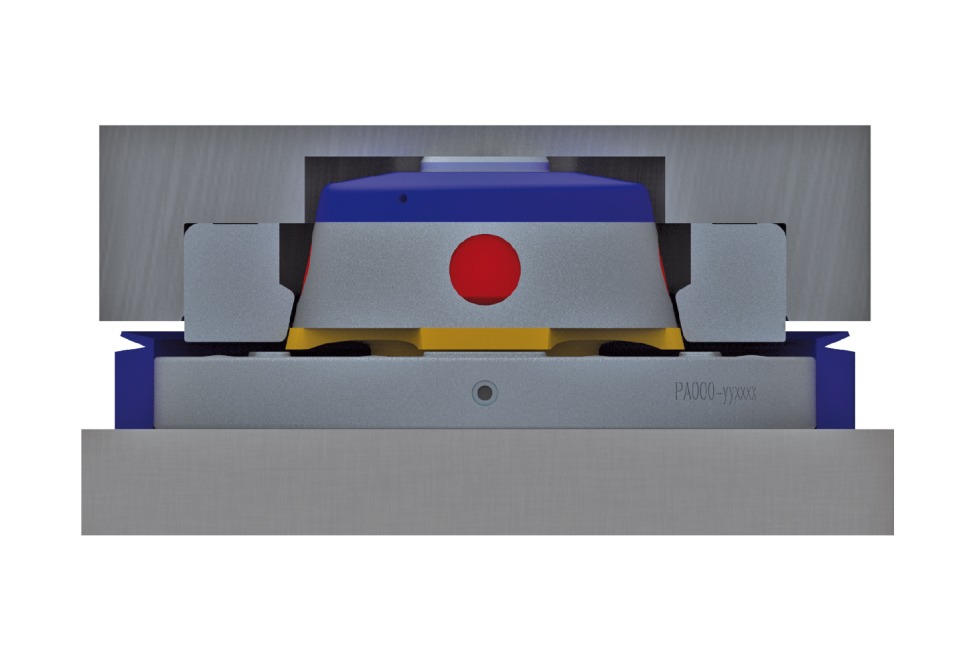
One-of-a-kind worldwide
Even tilted pallets safely reach their destination during feeding. This capability ensures that, regardless of their position, the pallets can be accurately and efficiently loaded into the system. The design allows for smooth operation, minimizing the risk of misalignment or damage, thereby streamlining the feeding process and enhancing overall productivity.
Disadvantage of classical clamping systems:
Many classical clamping systems have rigid, protruding chucking bolts (SK-principle). There is always a risk of damaging Z-reference surfaces during loading and unloading. By placing pallets on the chucking bolts they can easily loose their zero point. Compensation of thermal changes is not possible. The result: permanent zero point displacements.
Tolerance-freecentering
Advantages of GENIUS GRIP
- With a large pre-centring via the clamping bolt cage, damage to whatever reference surfaces is excluded during loading and unloading.
- GENIUS GRIP positions tolerance-free thanks to axially resilient centring lips (HSK-principle). The lift-off function lifts the pallets by 2.2 mm. Reference surfaces only come into contact during the clamping process.
- Thermal changes are compensated by the GENIUS GRIP system without zero point displacements..
- There is no lost of reference when the pallets are parked or stored.
- Even tilted or diagonally fed pallets find their destination safely with GENIUS GRIP.
No one else in the world offers you these advantages.
Thermal expansion
Classical clamping systems
Our technique
Disadvantage of classical clamping systems:
Many classical clamping systems have rigid, protruding chucking bolts (SK-principle). There is always a risk of damaging Z-reference surfaces during loading and unloading. By placing pallets on the chucking bolts they can easily loose their zero point. Compensation of thermal changes is not possible. The result: permanent zero point displacements.
Process safety
Advantages of GENIUS GRIP
- GENIUS GRIP centers backlash-free via axially resilient centering lips (HSK-principle).
- GENIUS GRIP automatically compensates for thermal warping. The zero point remains unchanged in the centre of the system.
- The island-shaped Z-reference surfaces are automatically cleaned.
- High process reliability during automation due to system controll via z-references.
- No dirt-prone internal clamping mechanism.
- Doublesided hardened and rust-free reference surfaces both in the pallet and the clamping system.
The result: GENIUS GRIP delivers a very high precision, especially in 5-axis and mill-turn operations.
Modularity
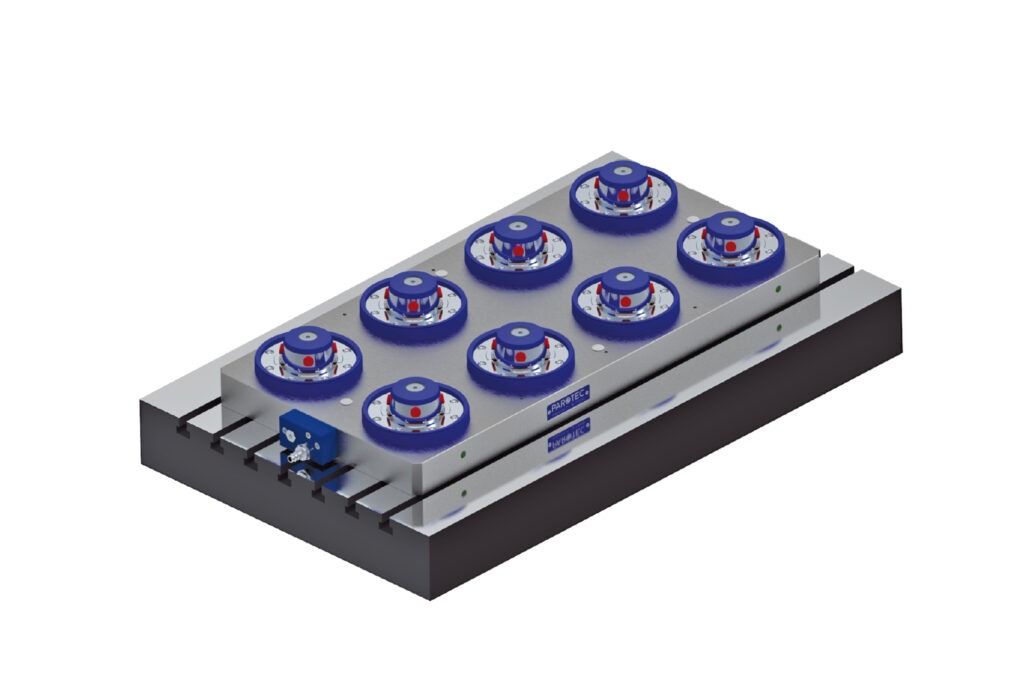
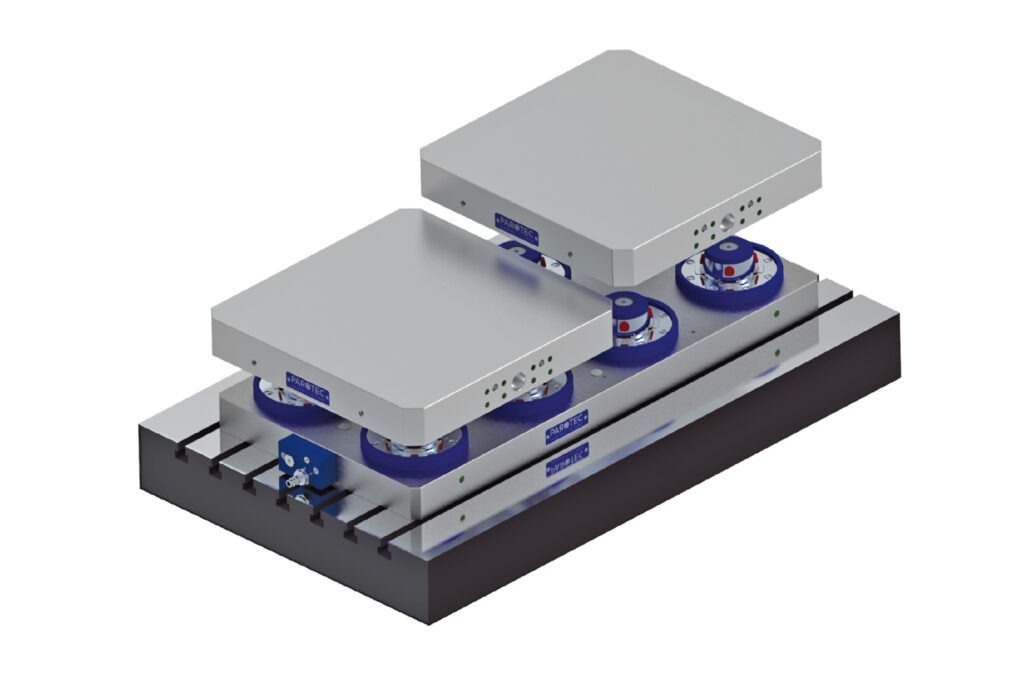
Example: GENIUS GRIP pallet x8
Example: GENIUS GRIP pallet x12
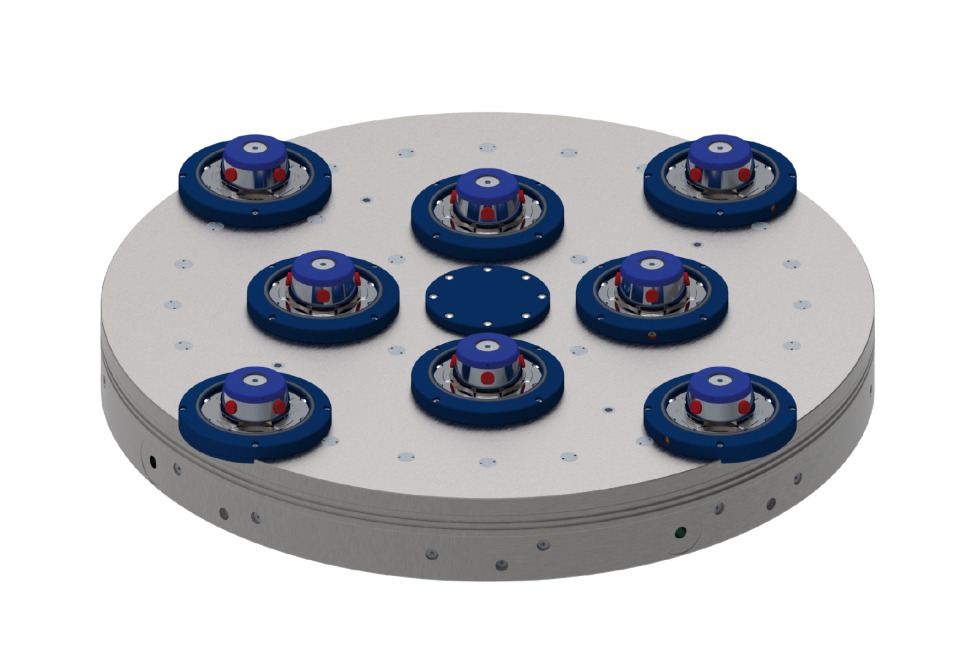
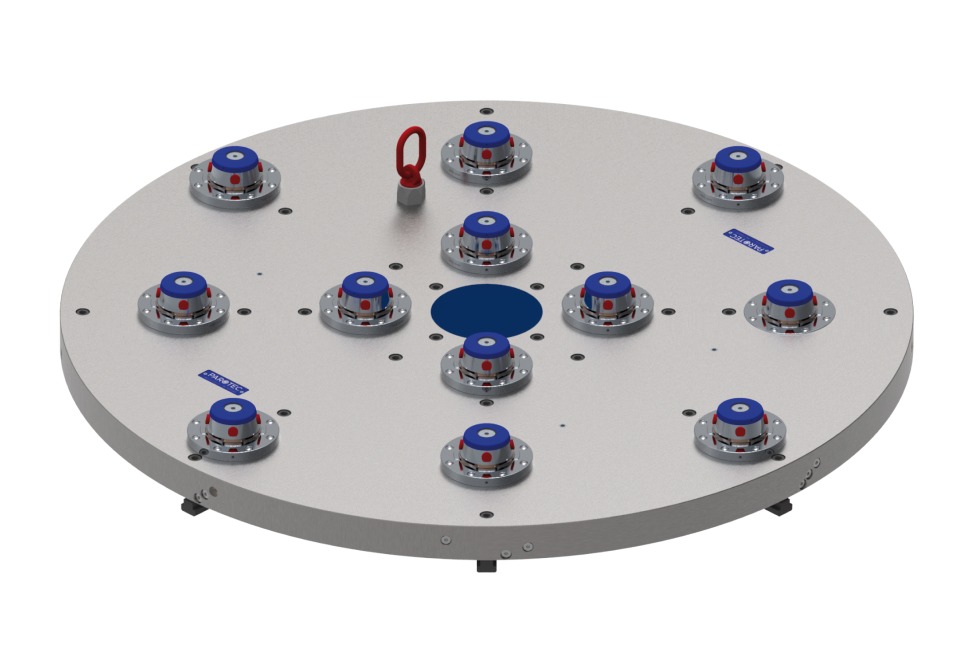
Advantages of GENIUS GRIP
- GENIUS GRIP clamping systems are available in differnt sizes and designs.
- GENIUS GRIP pallets can be combined with each other (see illustration on the left).
- GENIUS GRIP can be adapted to machine and workpiece sizes.
Maintenance
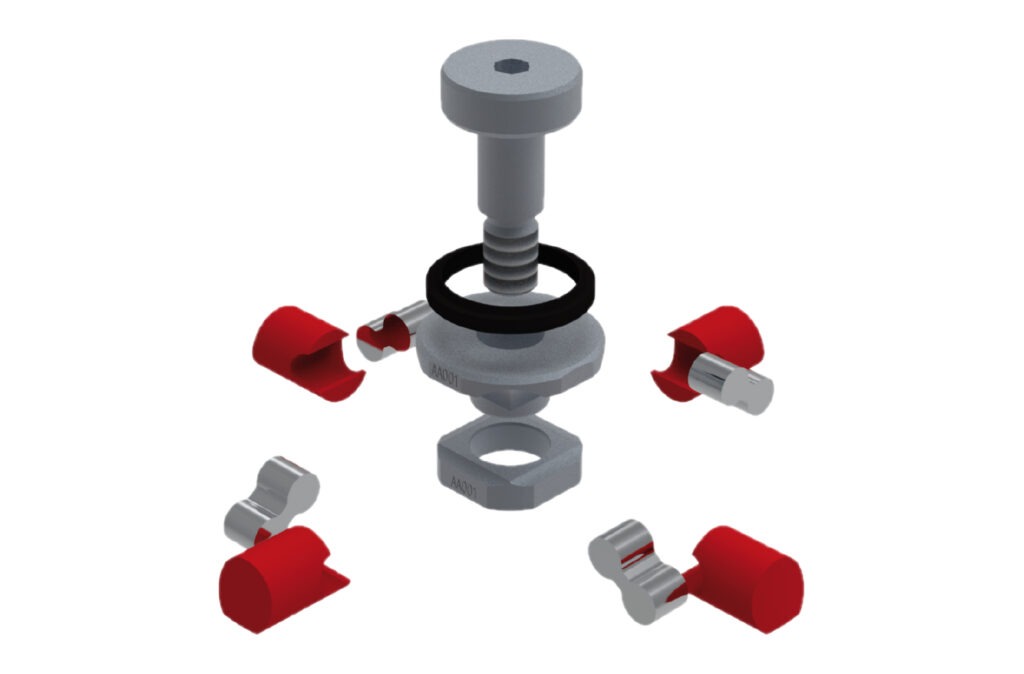
Advantages of GENIUS GRIP:
- Cleaning and maintenance of the clamping system is possible from the outside without loss of zero point and disassambly of the clamping system.
- No expensive specialist personnel is requiered for cleaning and maintenance. The work can be carried out in the shortest possible time by the operator of the machine.
- GENIUS GRIP is completely rust-resistant – thus no corrosion and minimum wear.
- Machine downtime due to contamination or wear is almost impossible.
Consistency
Disadvantages of classic clamping systems:
- Verschiedene oft nicht kompatible Systeme für unterschiedliche Fertigungs- und Bearbeitungsverfahren.
- Teilweise feste Systemgrößen.
Advantages of GENIUS GRIP:
- Variable Systemgrößen und Stichmaße bieten maximale Modularität
- GENIUS GRIP passt sich Ihrer Werkstückgröße sowie an vorhandene und neue Maschinen problemlos an.
- Optimale Durchgängigkeit durch ein einziges, immer kompatibles System für alle Fertigungs- und Bearbeitungsverfahren
Download Brochure
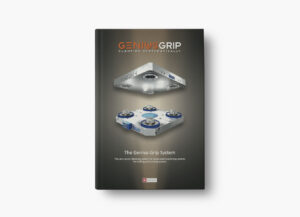