Palletizing systematically
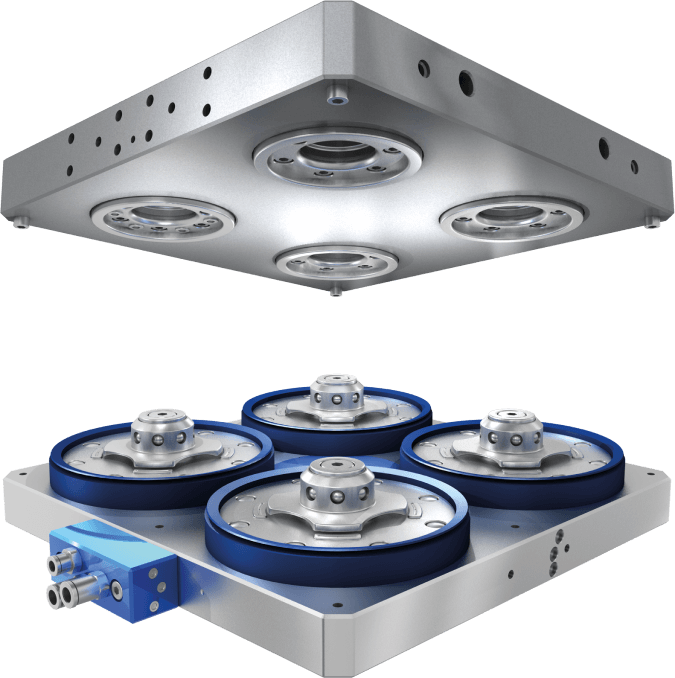
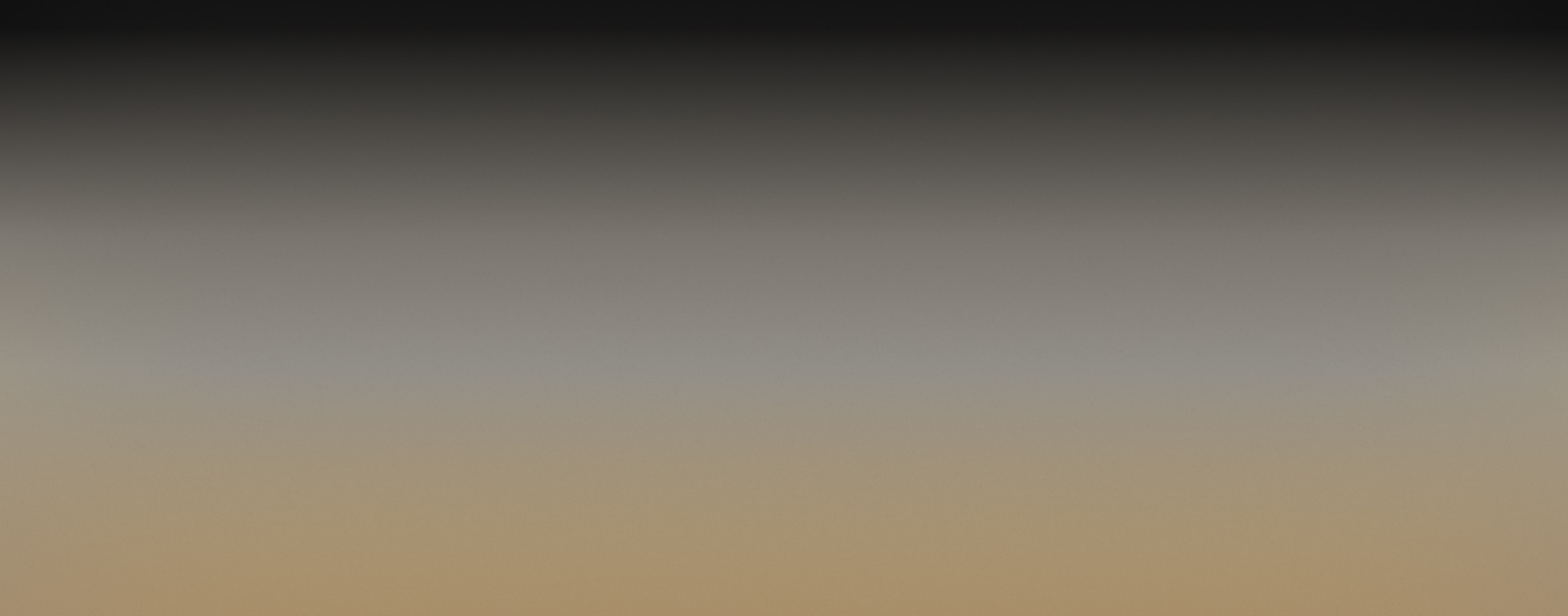
The continuous zero-point clamping system for all machining processes with a single interface.
1. Modular and compatible
With various grid sizes of e.g. 160 mm, 200 mm and 320 mm, you can effortlessly implement all your technical requirements. With POWER GRIP your devices are no longer confined to individual machines. Once components have been mounted, they can easily be swapped in and out. POWER GRIP does not loose its zero-point even if you have to swiftly produce something else in the meantime.
2. Easy automation.
POWER GRIP adapts effortlessly to any manufacturing processes, including automated ones, and renders your assembly as flexible as you wish.
Up to 45% more efficiency
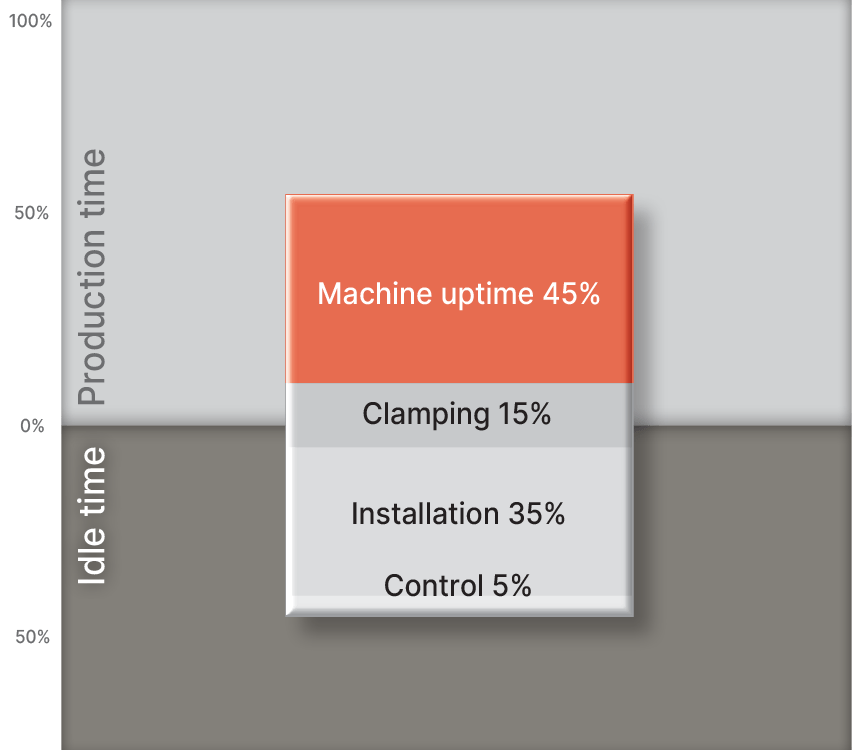
- Uneconomic manufacturing
- Non-optimized manufacturing processes
- No standardization
- High costs per unit
- Excessive delivery times
- Unfulfilled delivery dates
- High error rate
- Pricing pressure and competitive pressure
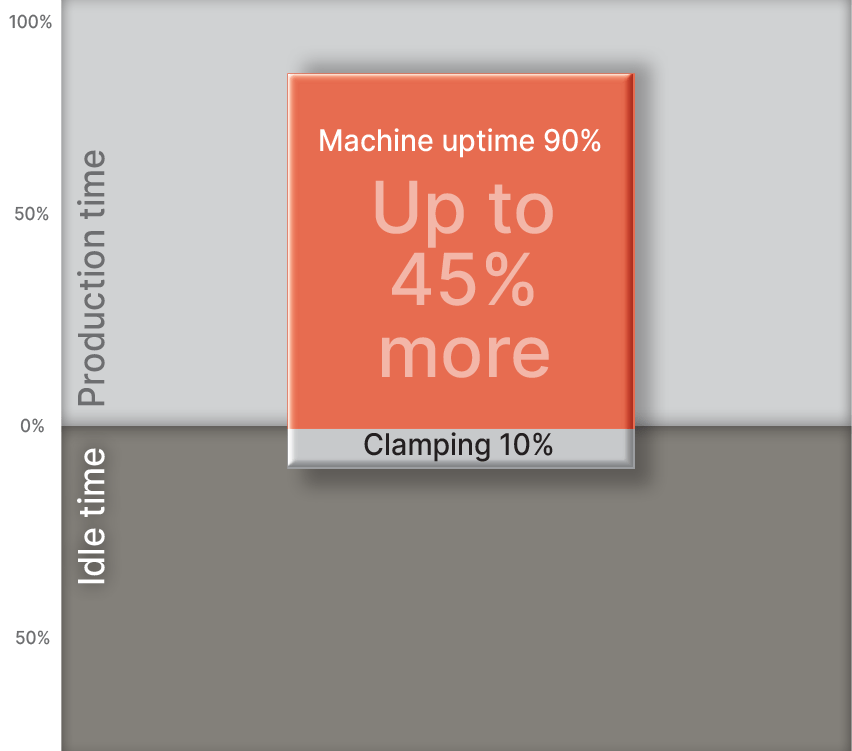
- Higher productivity and income
- Optimized manufacturing processes
- Standardized interfaces
- Low unit costs
- Reduced delivery times
- Adherence to delivery dates
- Low error rate
- Competitive capacity
10 Advantages at a Glance
Loading
With POWER GRIP you choose double integrated safety.
During the pallet loading process, a substantial lateral offset can be managed without any risk of damage to the sensitive Z-reference surfaces. This ensures precise handling and maintains the integrity of these critical contact points. A well-designed positioning aid significantly simplifies the loading process by ensuring accurate alignment and reducing the effort required for proper placement. The pallet is initially prepositioned to ensure accurate alignment. Thanks to the lifting function, the reference surfaces remain completely untouched at this stage, preventing any potential damage and ensuring precise positioning.
Pre-centering and Loading
Classic palletizing systems
POWER GRIP technology
- Possibility of Z-reference surface damage during pallet loading and unloading
- Z-reference surface damage avoidance during pallet loading and unloading
- During pallet loading, damage is pre-programmed, since the pallet collides with the Z-reference surfaces as soon as it is loaded.
- Whilst the pallet is being loaded, the risk of damage is excluded since the pallet is lifted by 2 mm
- Pallets with chucking bolts can easily loose their references when being parked.
- Since there are no chucking bolts, there is no reference loss.
Maintenance
In contrast to other palletizing systems, all important wear parts of the POWER GRIP system are accessible from the outside. The system is easy to clean. Complete disassembly is unnecessary. The zero-point is not lost. This process only requires little time. With POWER GRIP, there is no risk of idle time due to dirt or abrasive wear.
Maintenance and Cleaning
Classic palletizing systems
POWER GRIP technology
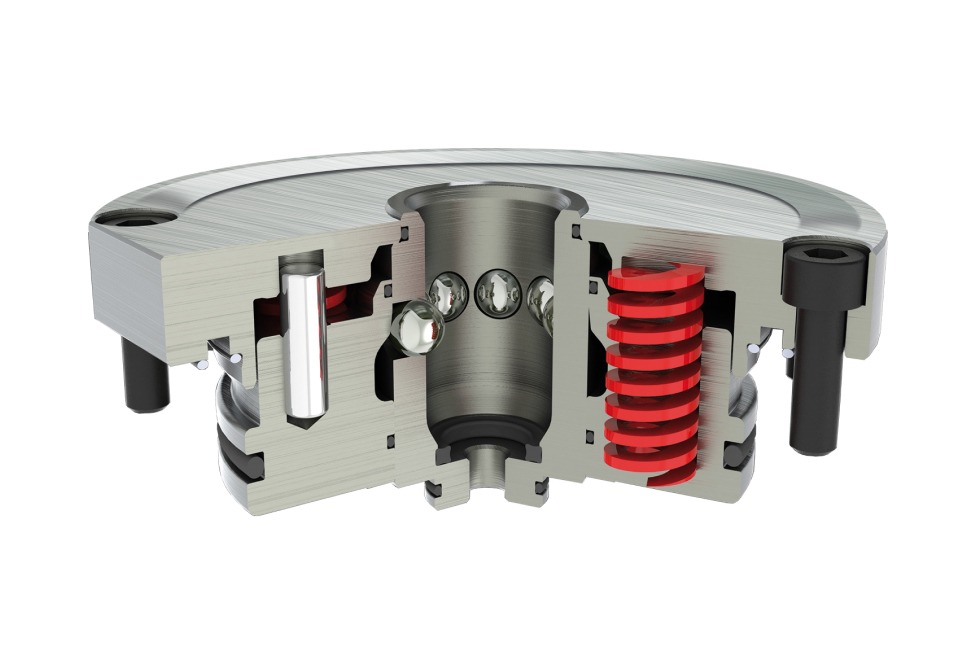
- Higher investment of time and cost during servicing.
- The dirt can lead to system blockages.
- No process safety.
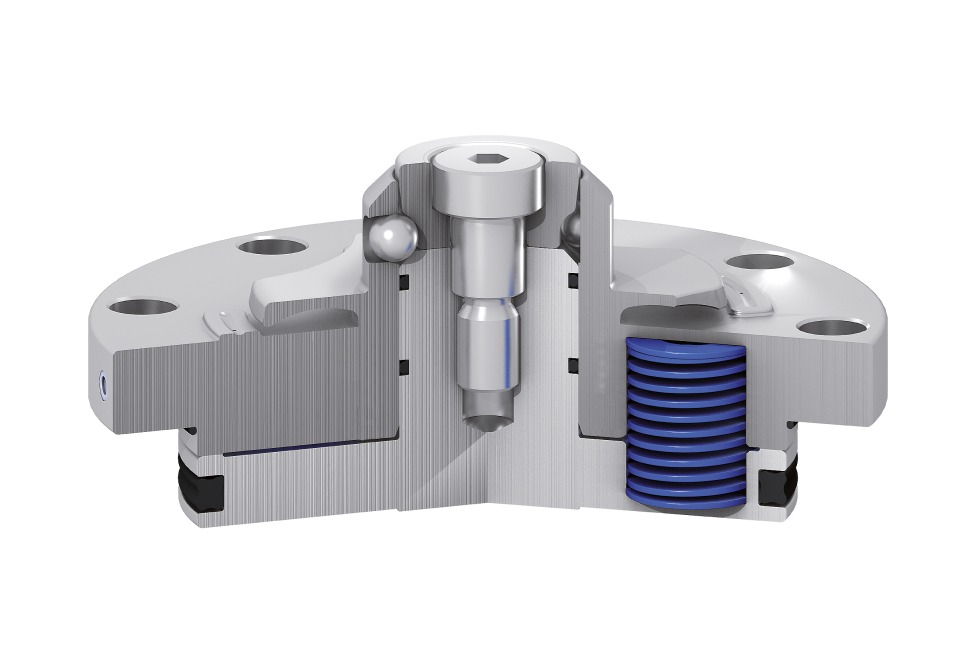
- Reduced cleaning time and expenditure.
- Maintenance „without zero-point loss“ within very little time.
- High process safety.
Accuracy
Accurately repeatable.
System accuracy.
Accuracy
Classic palletizing systems
POWER GRIP technology
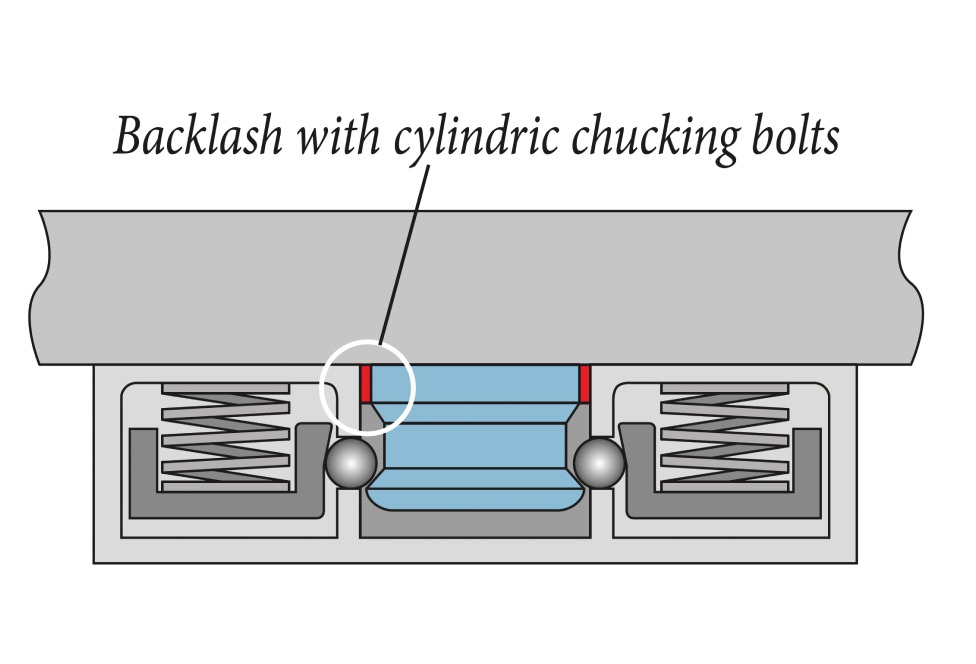
- For classic palletizing systems, there is a certain amount of backlash between chucking bolts and reference holes due to manufacturing tolerances. It measures between 0,005 and 0,01 mm.
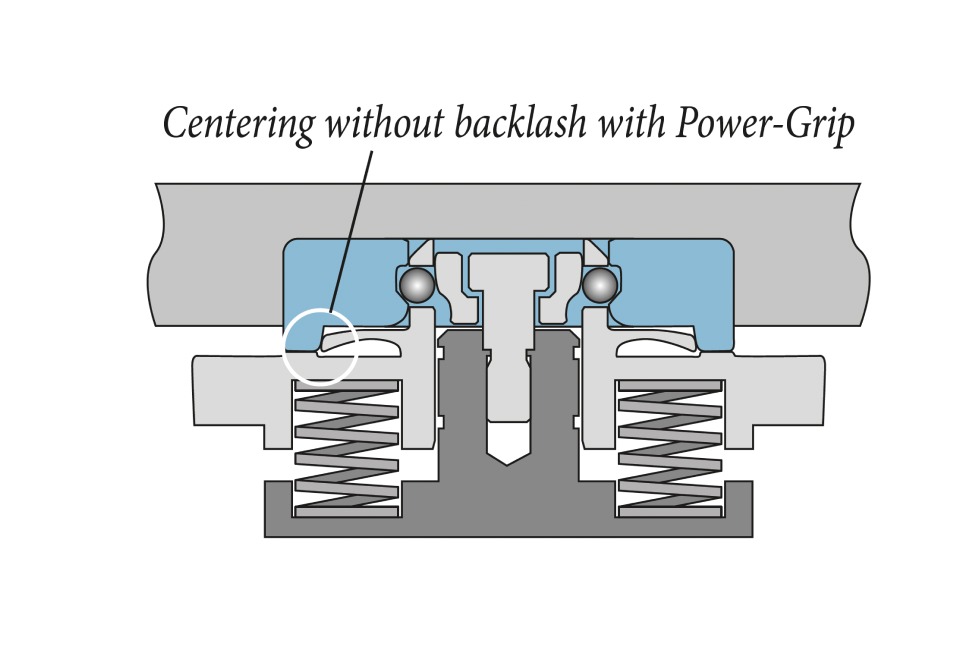
- Four axial centering spring lugs guarantee tolerance-free centering
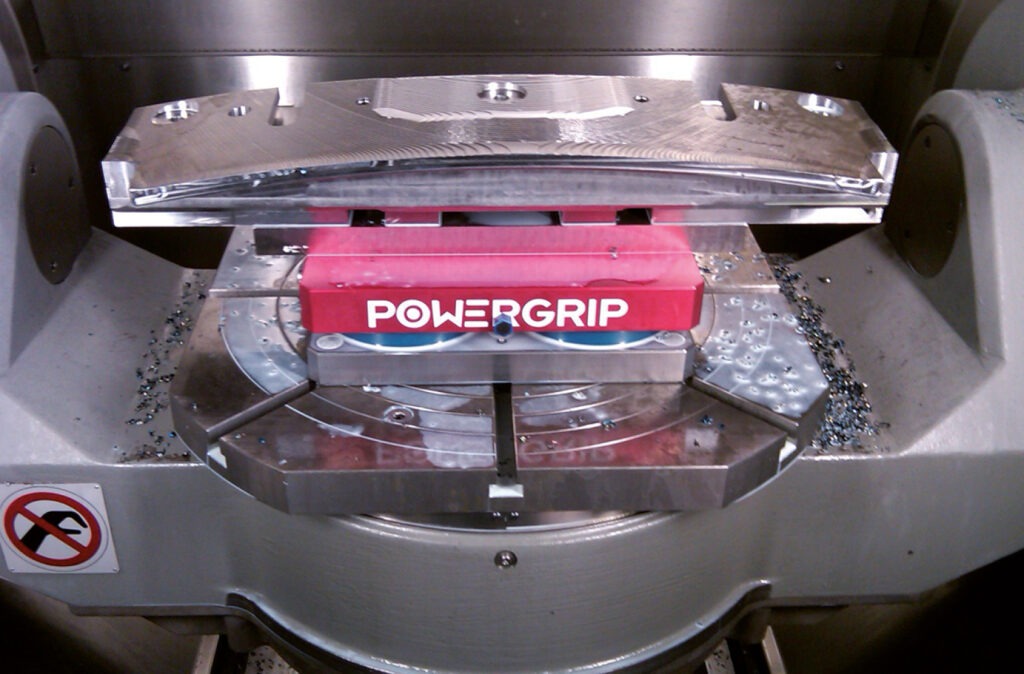
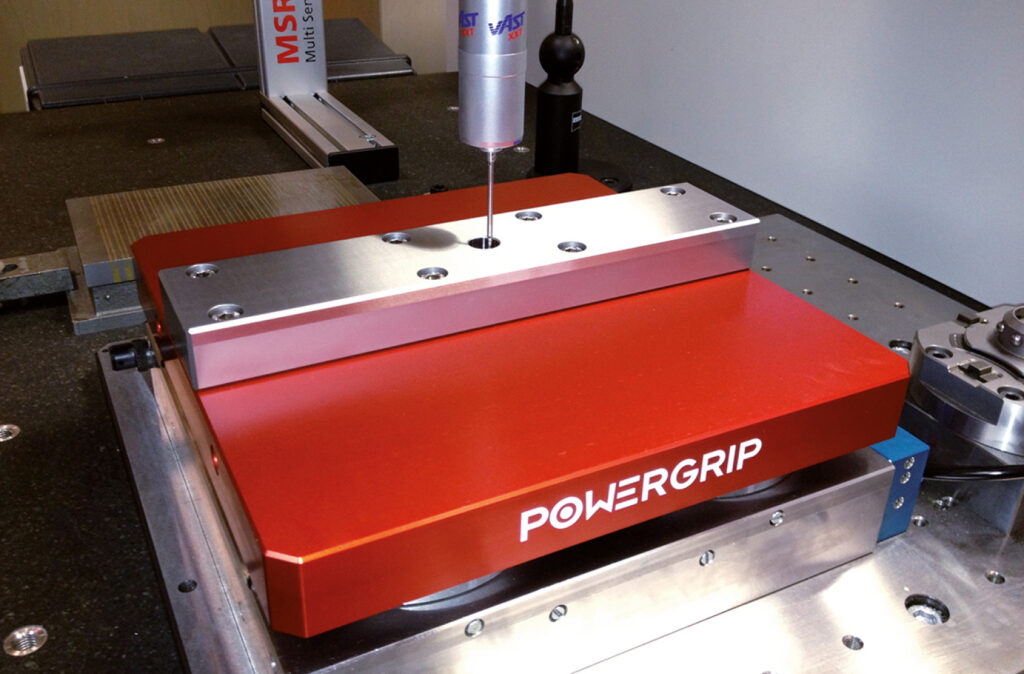
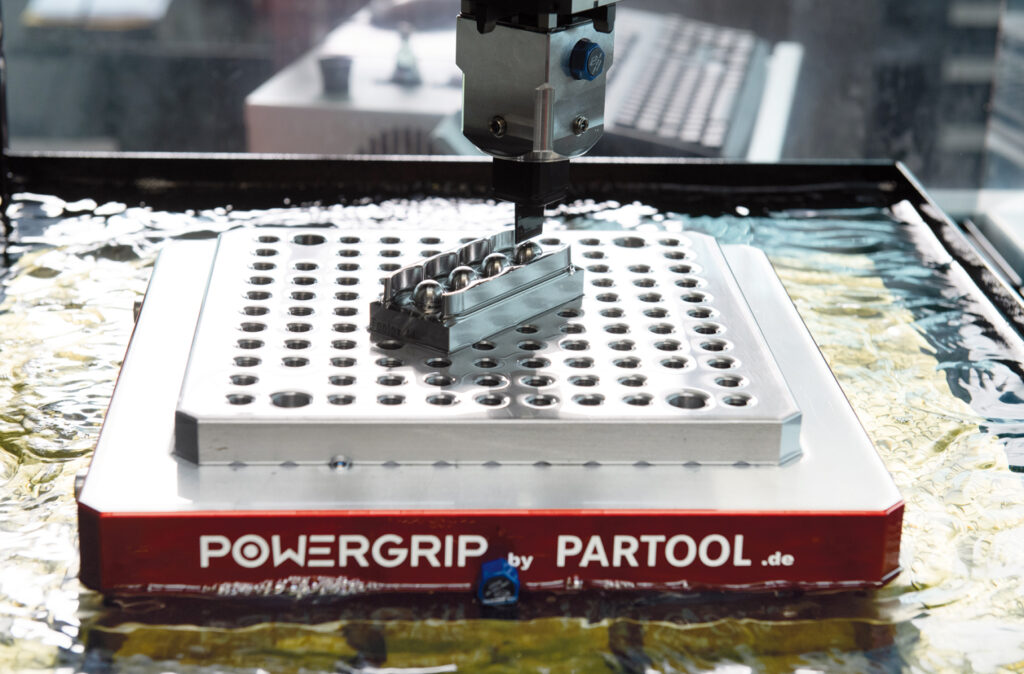
Thermal Expansion
Conventional clamping systems
POWER GRIP Technology
Positioning
Classic palletizing systems
POWER GRIP technology
- Positioning only by reference and compensation bolts.
- At least 3 kinds of chucking bolts are necessary: reference, compensation and chucking bolts, bolts for automation etc.
- The abrasive wear of rigid clamping components can lead to increased abrasive wear and therefore backlash.
- Centering is achieved across all centering sleeves.
- Only one kind of centering and clamping sleeve.
- Four axial centering spring lugs do not allow abrasive wear and therefore no backlash.
Chucking
Classic palletizing systems
POWER GRIP technology
- Thermal variations cause irregular engagement of ball pivots/slide feeds.
- Ball pivots engage equally during thermal variations.
Thermal expansion compensation
Classic palletizing systems
POWER GRIP technology
- Centering offset during 5-axis processing
- No centering offset during 5-axis processing
Z-references
POWER GRIP is always equipped with a Z-reference cleaning system. Z-reference surfaces are cleaned at every chucking process. This is important for high levels of accuracy, process safety and lifespan. The hardened and rust-proof POWER GRIP reference surfaces, both in the palletizing system and the PG pallets, make this system virtually non-wearing and readily automatable.
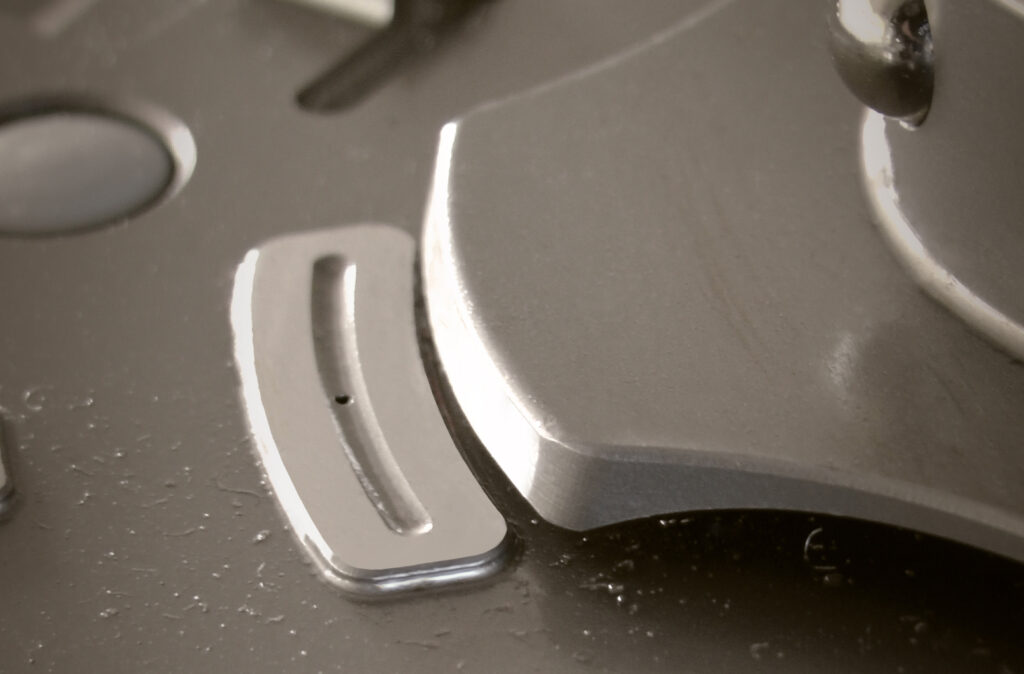
Z-references
Classic palletizing systems
POWER GRIP technology
Z-reference cleaning, Overpressure, Z-reference feedback
Classic palletizing systems
POWER GRIP technology
- Overpressure not possible
- Not automatable
- Modification for automation is very costly/might be impossible
- Overpressure available
- Z-reference feedback always possible for automation
- Modification for automation practicable within a few minutes and without specialists
Z-references
Classic palletizing systems
POWER GRIP technology
In a released state, a continuous flow of air effectively cleans and protects the Z-references from dirt and contamination. This airflow ensures that any debris or particles are blown away, maintaining the integrity and cleanliness of the reference surfaces. As a result, the system is kept in optimal condition, which contributes to its overall performance and reliability.
Process Safety / Automation
By means of hardened, rust-proof reference surfaces, both on the pallet and the pallet carrier, as well as by the additional possibility of monitoring by Z-reference feedback, POWER GRIP can be automated at any time.
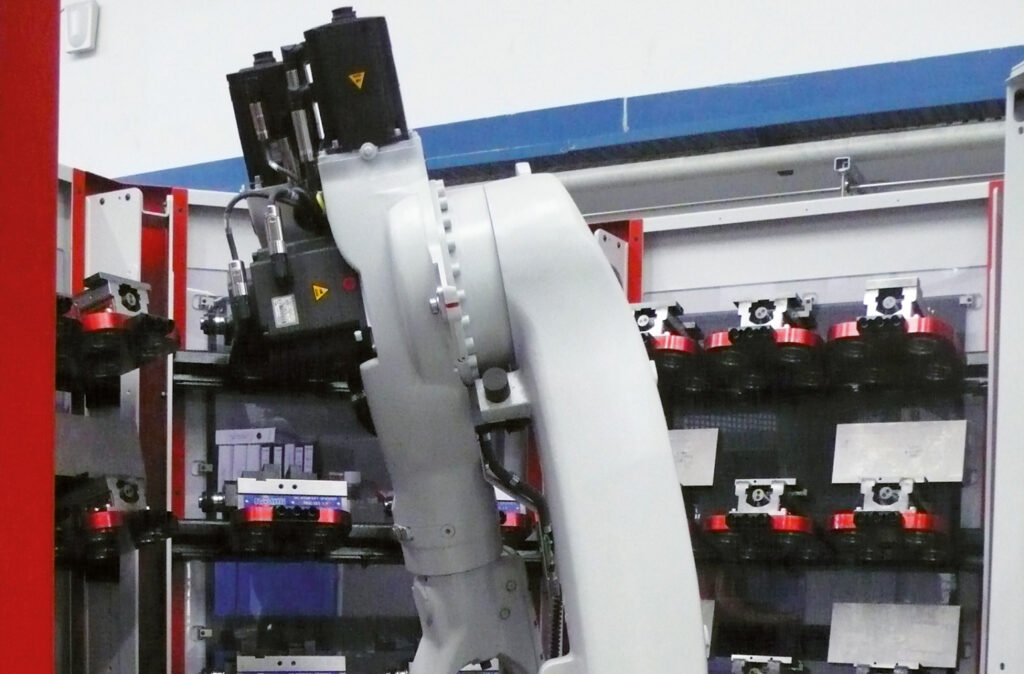
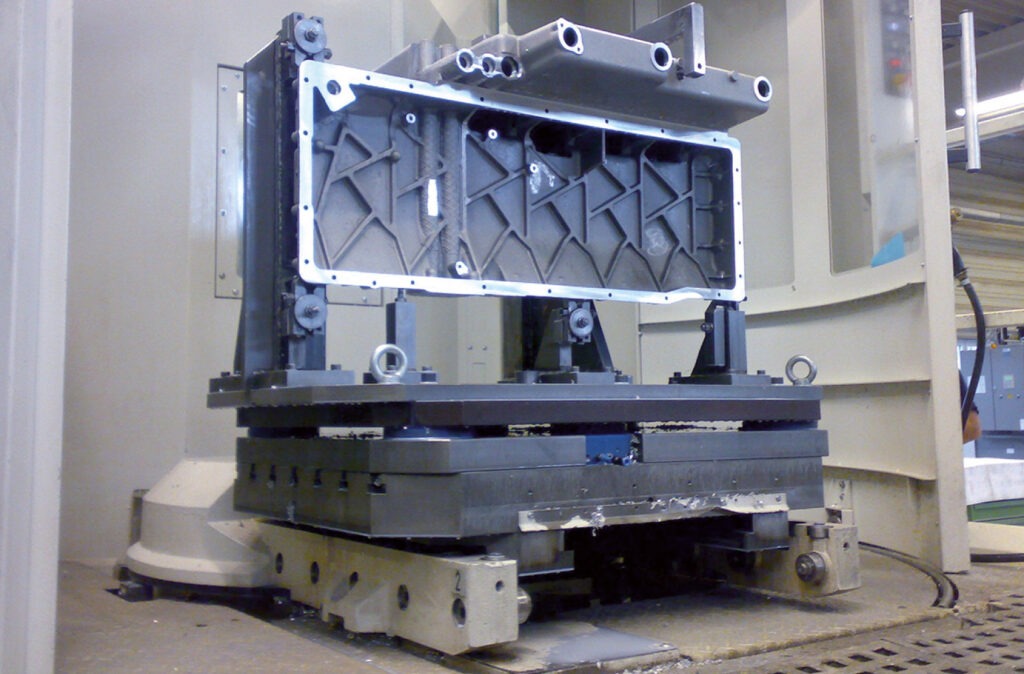
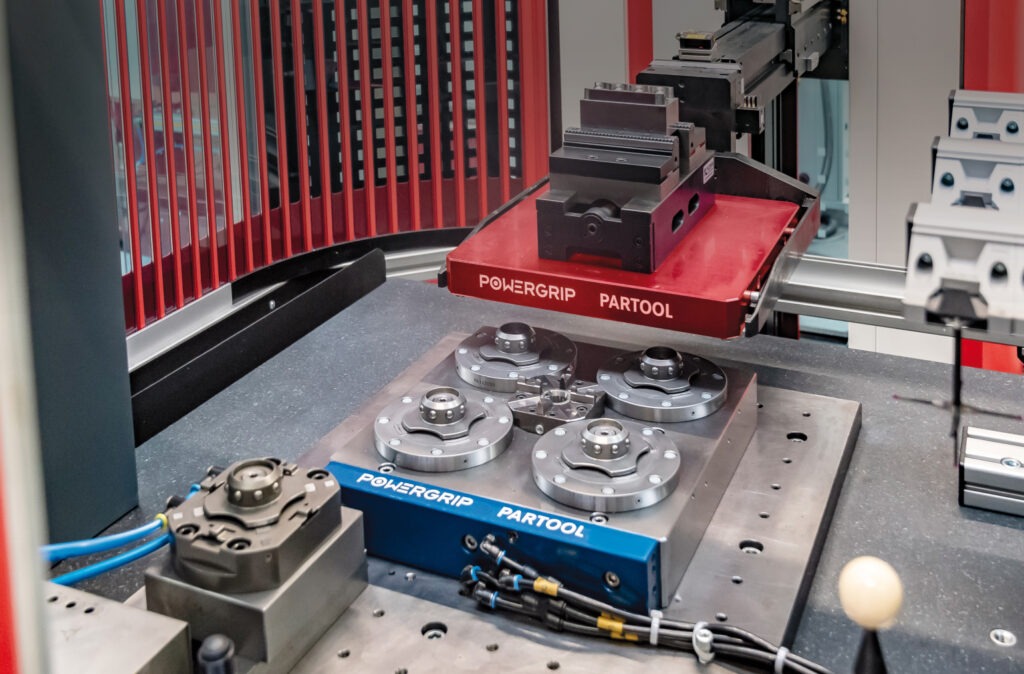
Automation
Classic palletizing systems
POWER GRIP technology
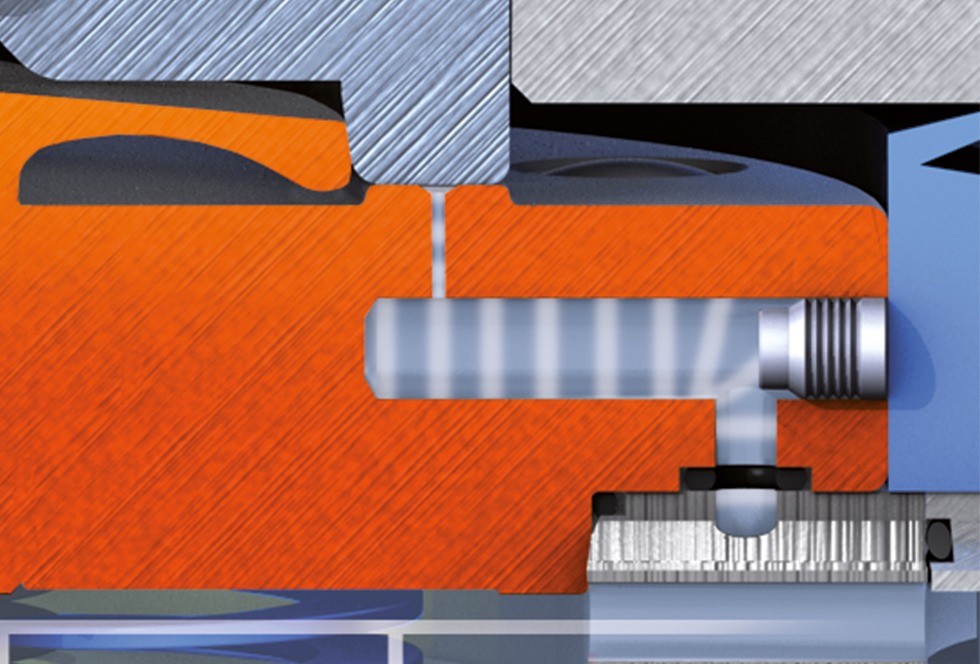
In a locked state, the airflow is interrupted, serving as a clear signal to the system that the pallet is securely clamped in place. This interruption indicates that the clamping process has been successfully completed, allowing production to commence. With the pallet firmly held, all machining operations can begin safely and efficiently, ensuring that the workpiece remains stable and accurately positioned throughout the production process.
The pallet of the classic clamping system normaly rests on the Z-references of the clamping module by it‘s own weight. Even if a chucking bolt is broken or does not exist any more the drill holes for the Z-reference feedback are still sealed. The pallet seems to be clamped mechanically but it isn‘t. The start signal for the beginning of processing can still be carried out. Tolerances during fabrication and variations in temperature cause additional problems. The positioning by conical chucking bolts can not be carried out exactly. Process safety does not really exist in the end.
POWER GRIP works different. The pallet does not contact the Z-references. Contact only takes place in the moment of clamping. The signal for „pallet clamped” only occurs if the centering spring lugs (7,5 KN each) are load-ed and the drilling holes of the Z-reference feedback are closed.
Z-reference feedback
Classic palletizing systems
POWER GRIP technology
Material, Endurance, Clamping Force
POWER GRIP is made of high quality materials. Each centering unit chucks automatically with a clamping force from 16,000 N up to 39,000 N. Even under high pressure, e.g. under high machining forces or during a machine crash, pallets cannot be ripped from the palletizing system.
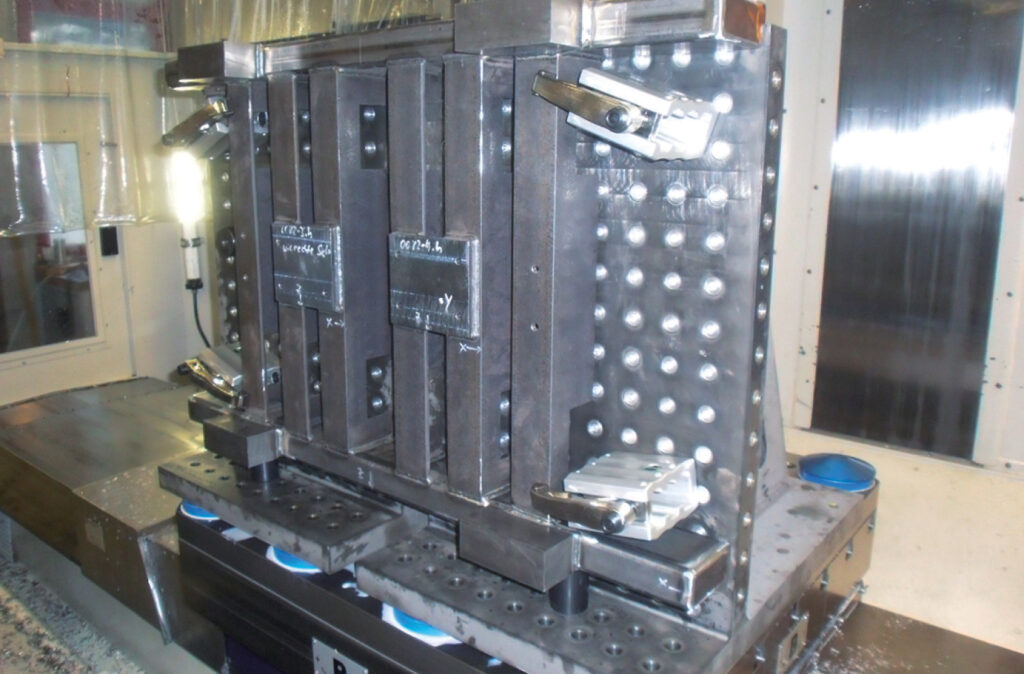
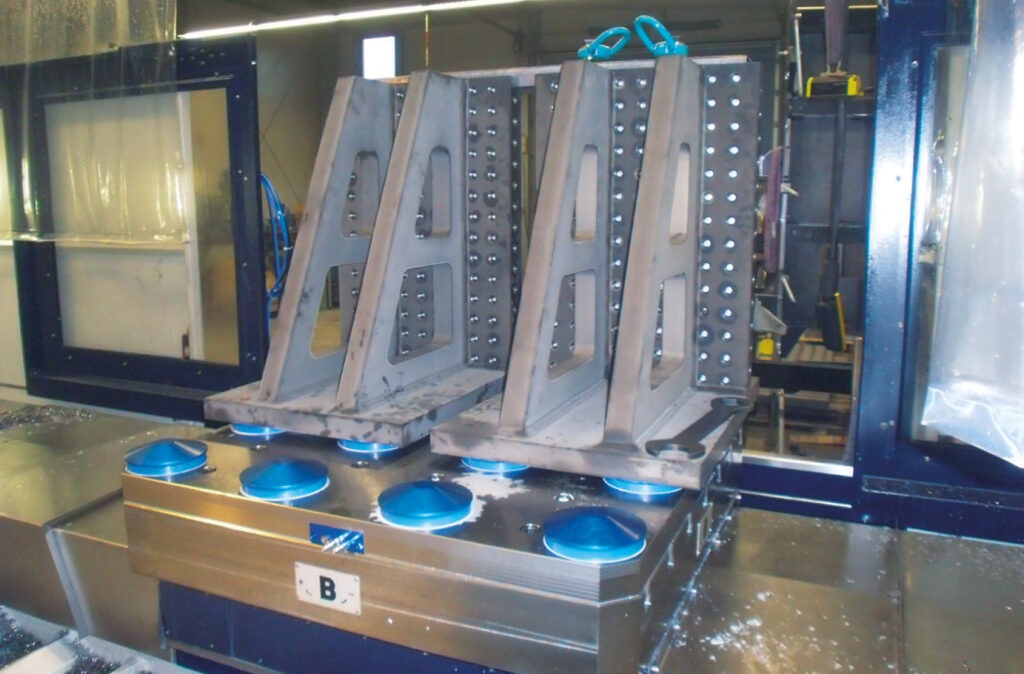
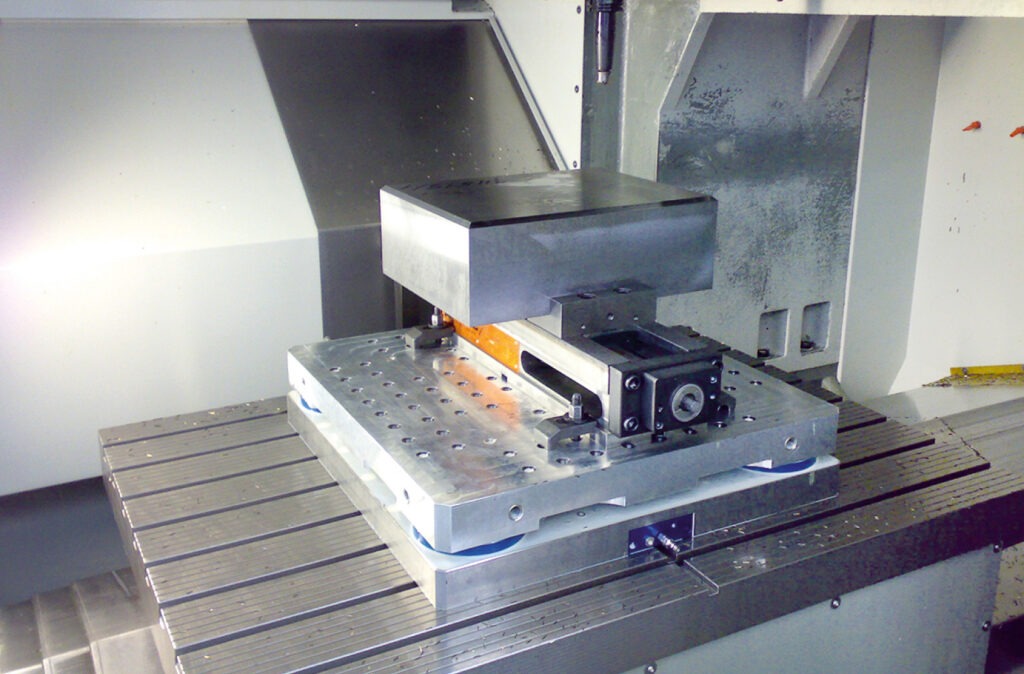
Material
Classic palletizing systems
POWER GRIP technology
The pallet carrier consists of 1.2085 steel, centering units as well as centering and clamping sleeves are made of rust-proof steel
Releasing and Clamping
Classic palletizing systems
POWER GRIP technology
Modularity and Consistency
Due to POWER GRIP’s modularity, the palletizing system can be adapted to various work piece sizes as well as to existing and new machines. POWER GRIP can be used for a variety of manufacturing processes. These include: 3- or 5-axis milling, EDM-ing, Measuring, Grinding, Lasering & Turning.
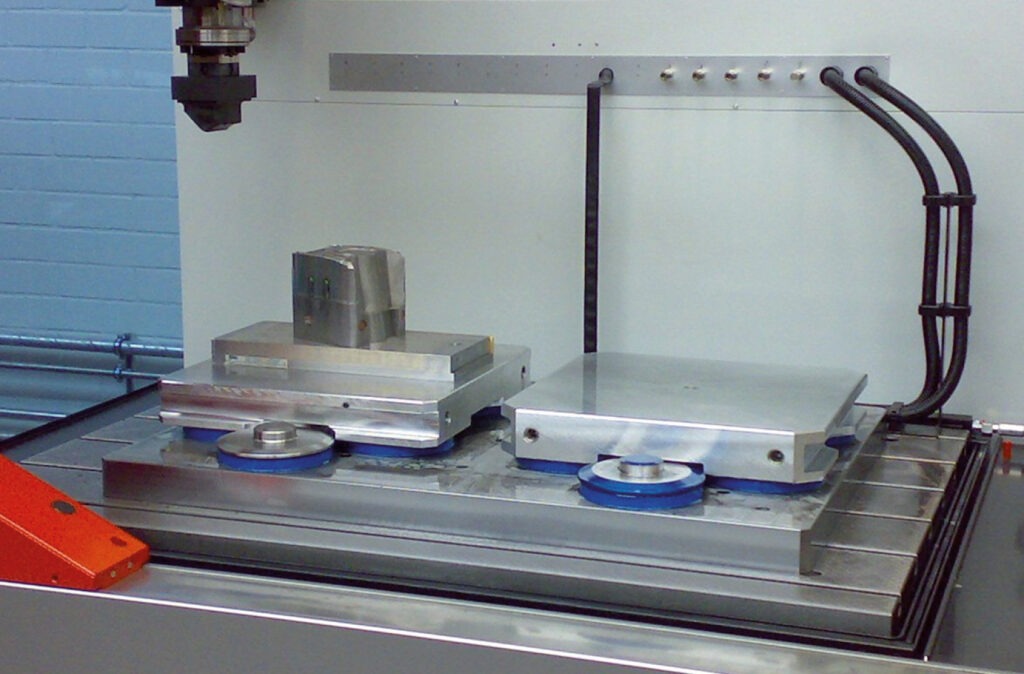
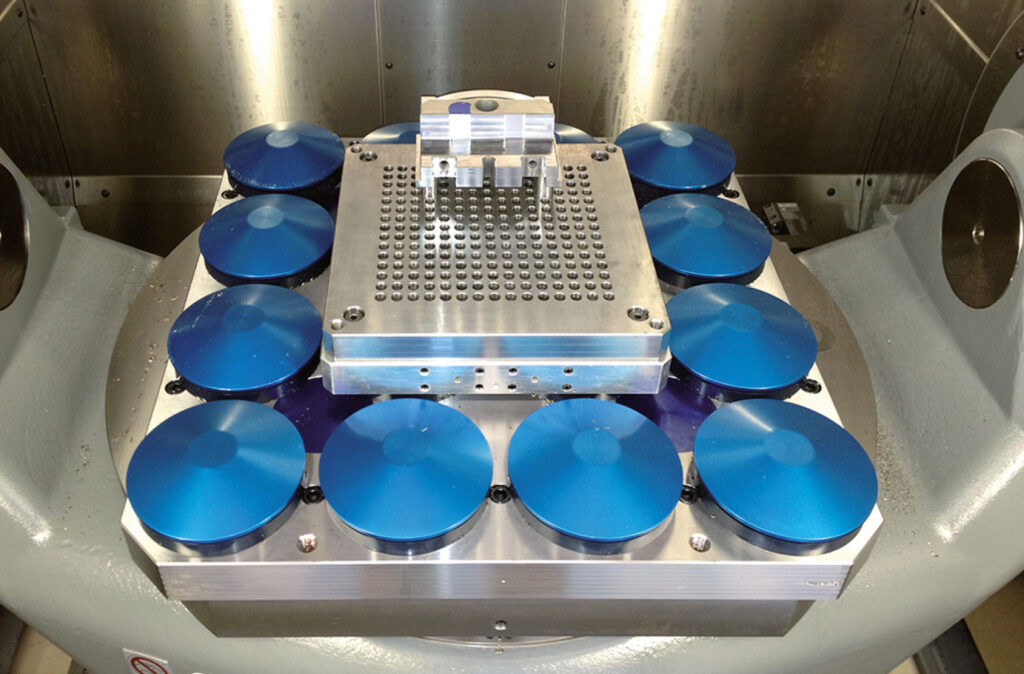
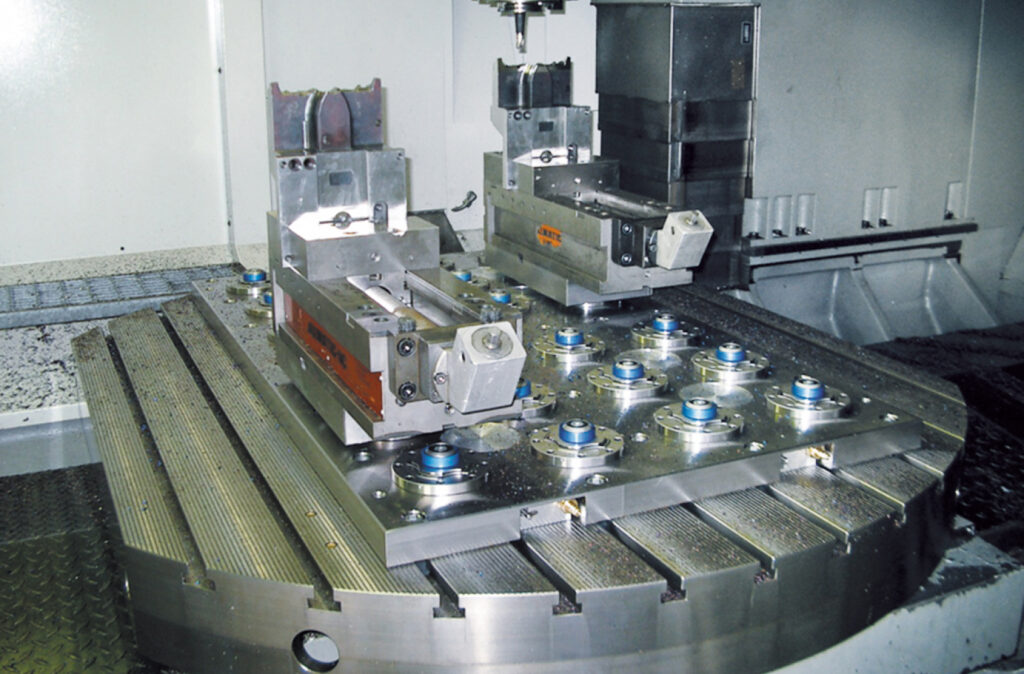
Modularity
Classic palletizing systems
POWER GRIP technology
Consistency
Classic palletizing systems
POWER GRIP technology
Investment and Gain
acquisition costs of your machine tool
Basic equipment ~ 15.000.- € and automation
Sum
[= total investment divided by 6]
[= (total investment x 4.5 %)÷2 ]
regarding occupancy cost of machine space
Maintenence costs
(Example B due to longer runtimes ca. 20% more)
(Example C due to longer runtimes ca. 40% more)
General share of wages
Sum of positions
Fixed costs/year divided by total runtime
(Ex. A: 80% , Ex. B: 65%, Ex. C: 50% of the wages / total runtime)
estimated share of expendable goods/hr.
estimated share of energy/hr.
Estimated share of varaible costs
Sum of positions
Fixed costs/hr. + variable costs/hr.
Hourly rate attainable on the market
attainable hourly rate/hr. minus production costs/hr.
difference derived from prod. costs and attainable hourly rate multiplied by total runtime
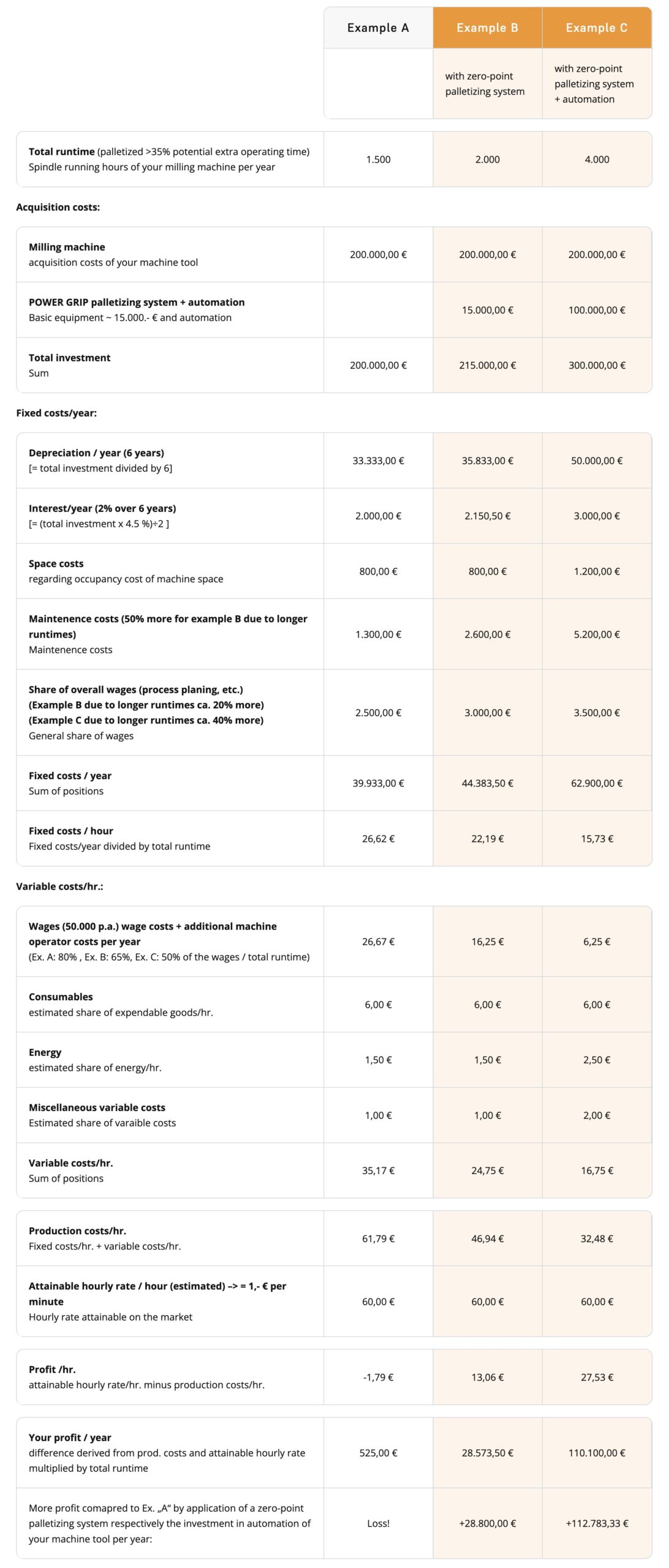
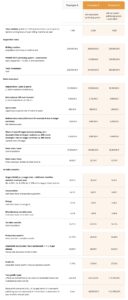
Sample Applications
POWER GRIP 1-fold
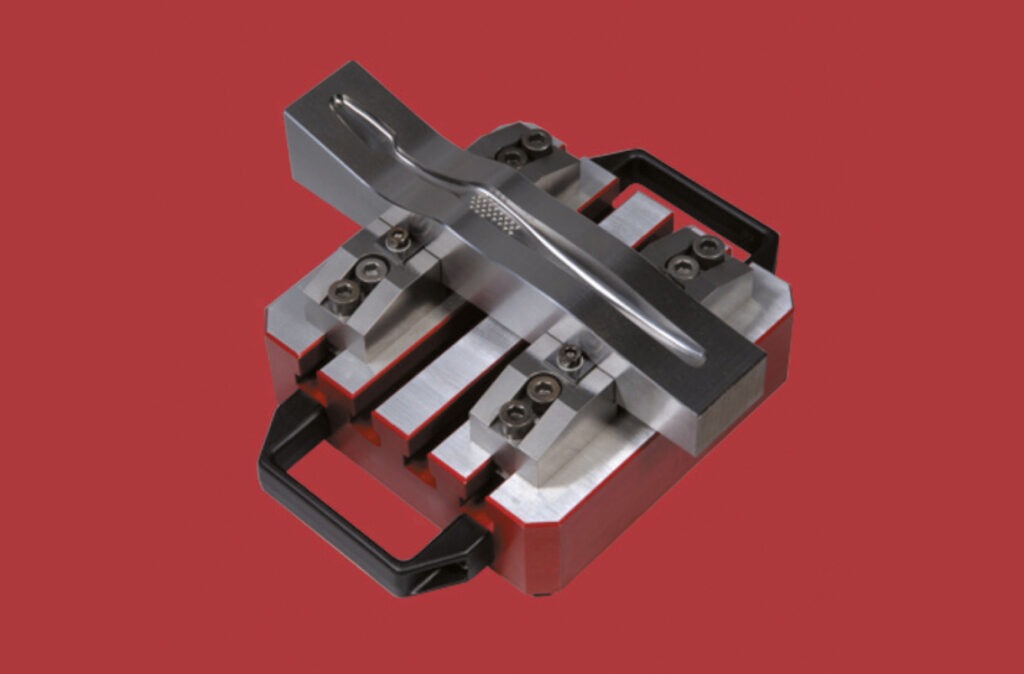
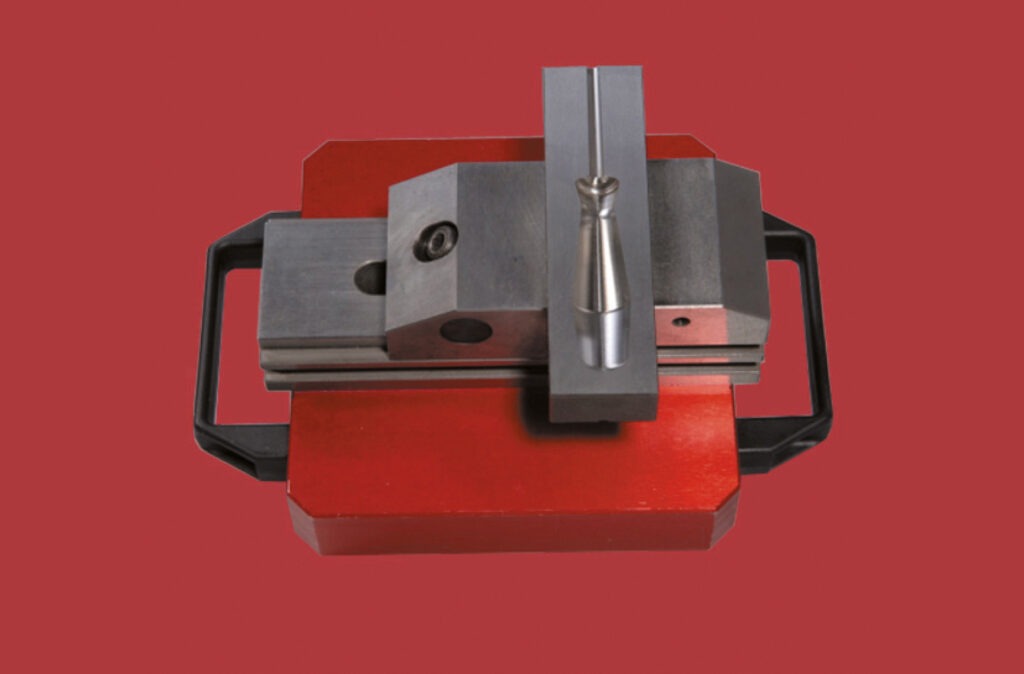
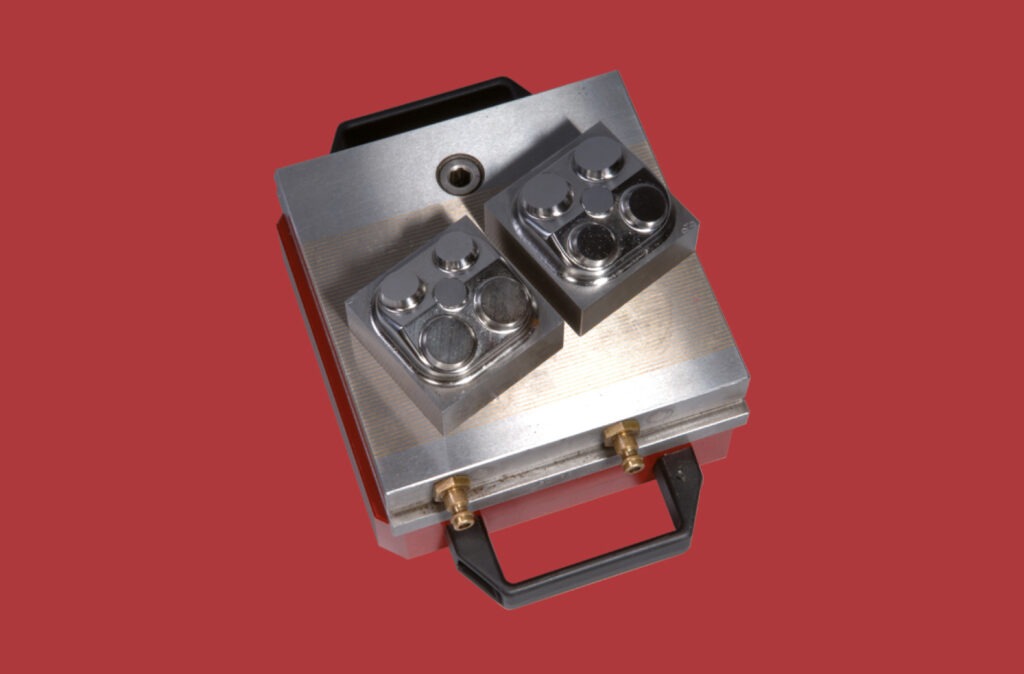
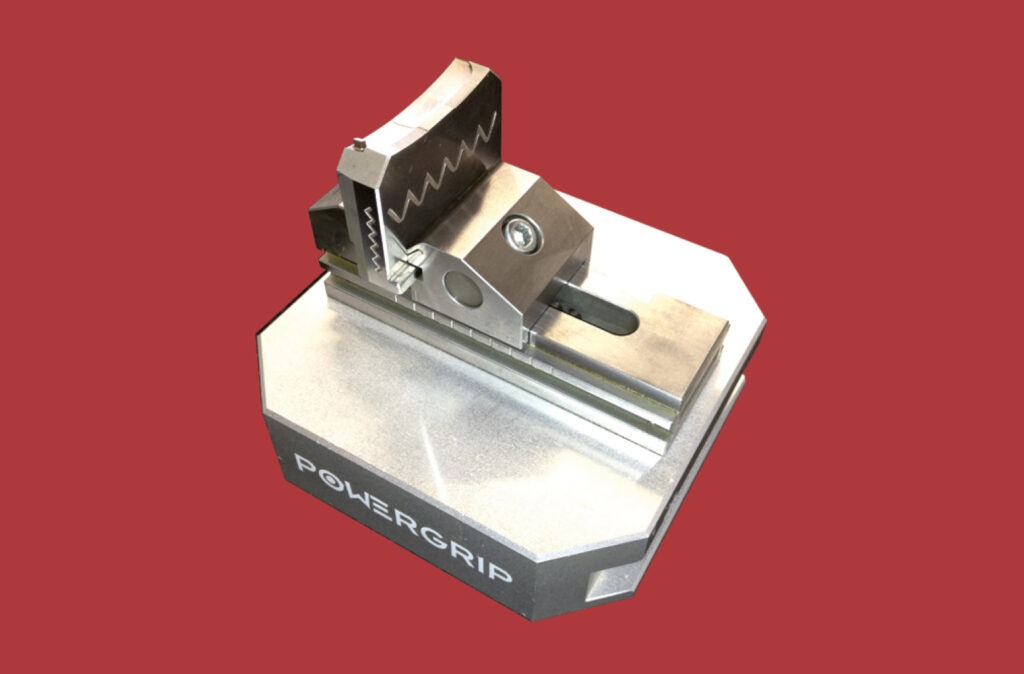
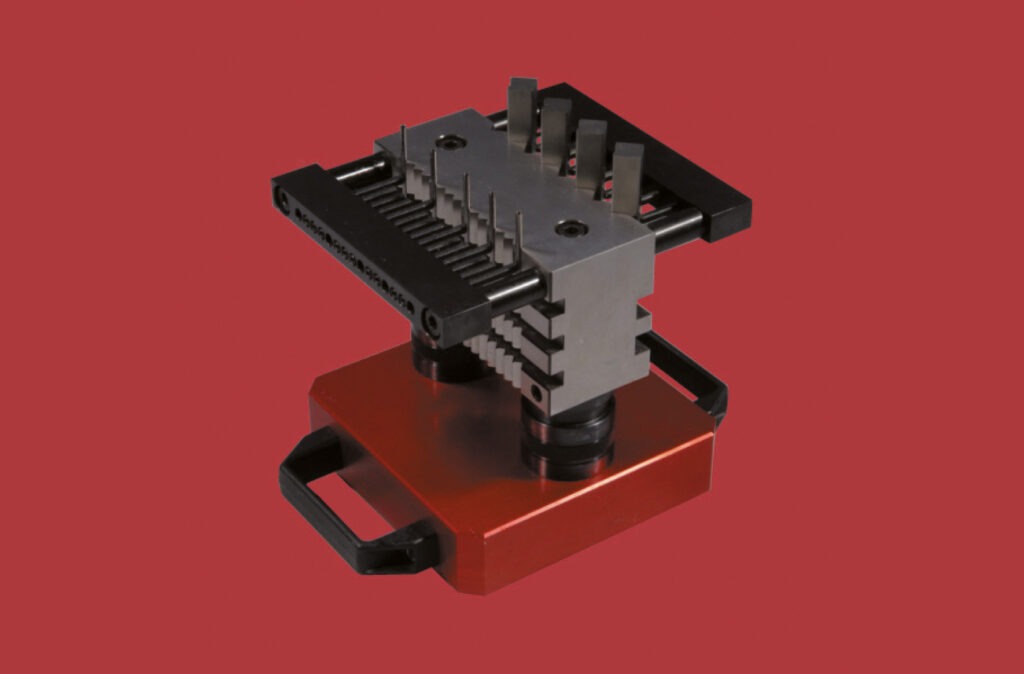
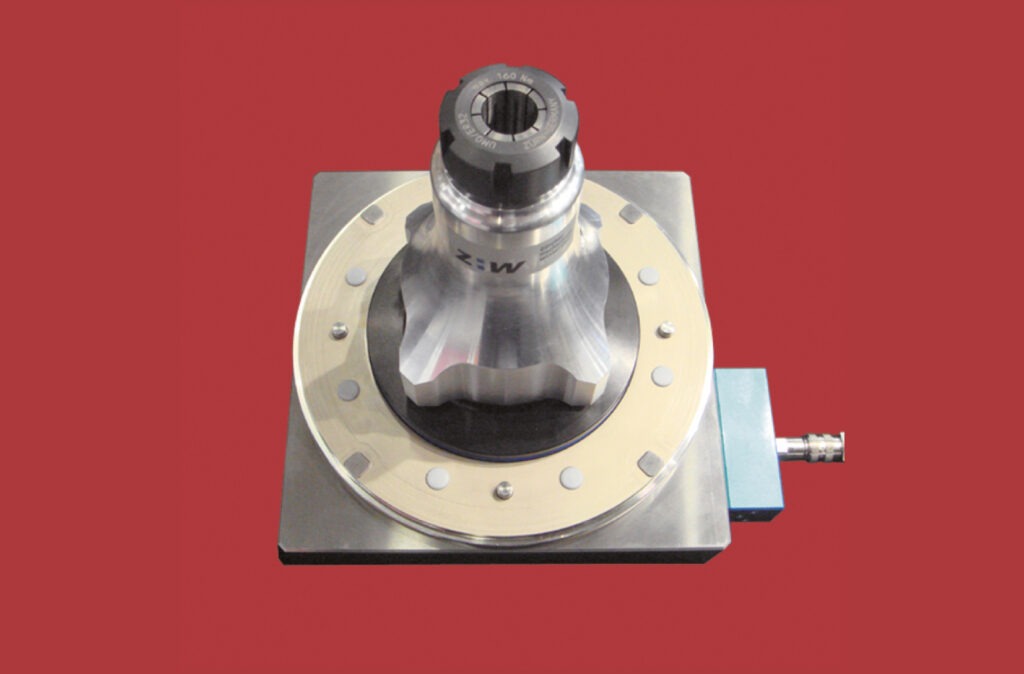
POWER GRIP 2-fold
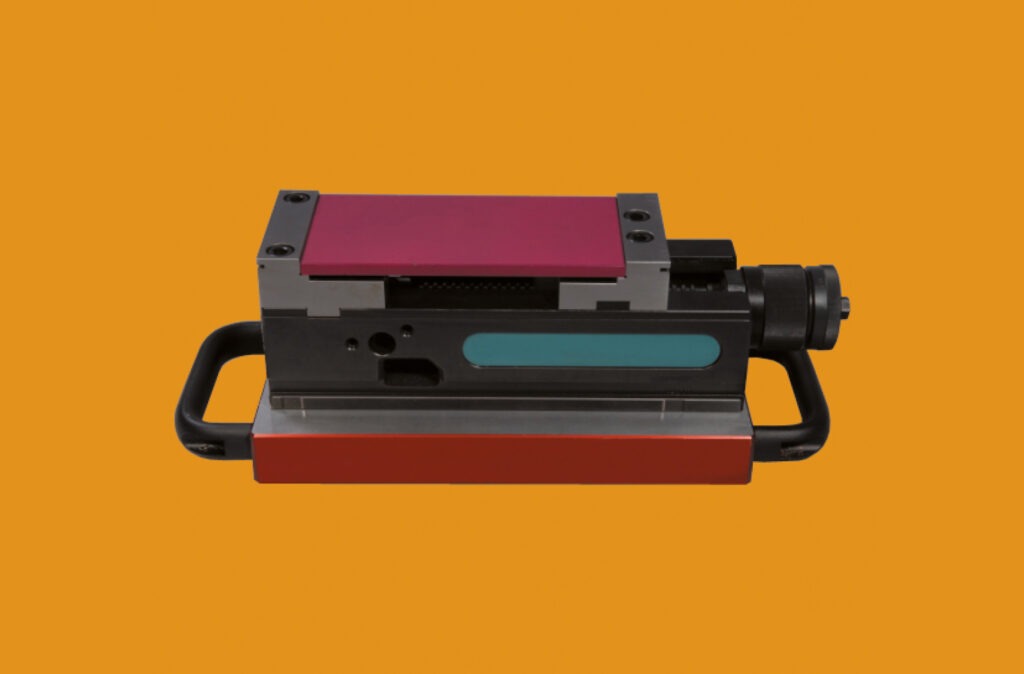
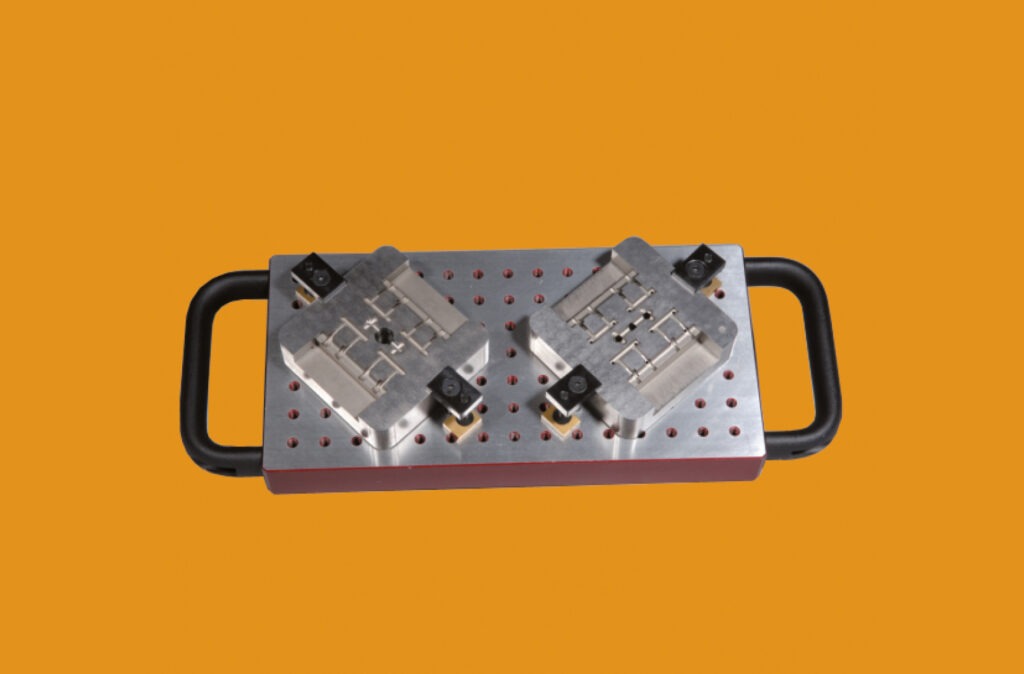
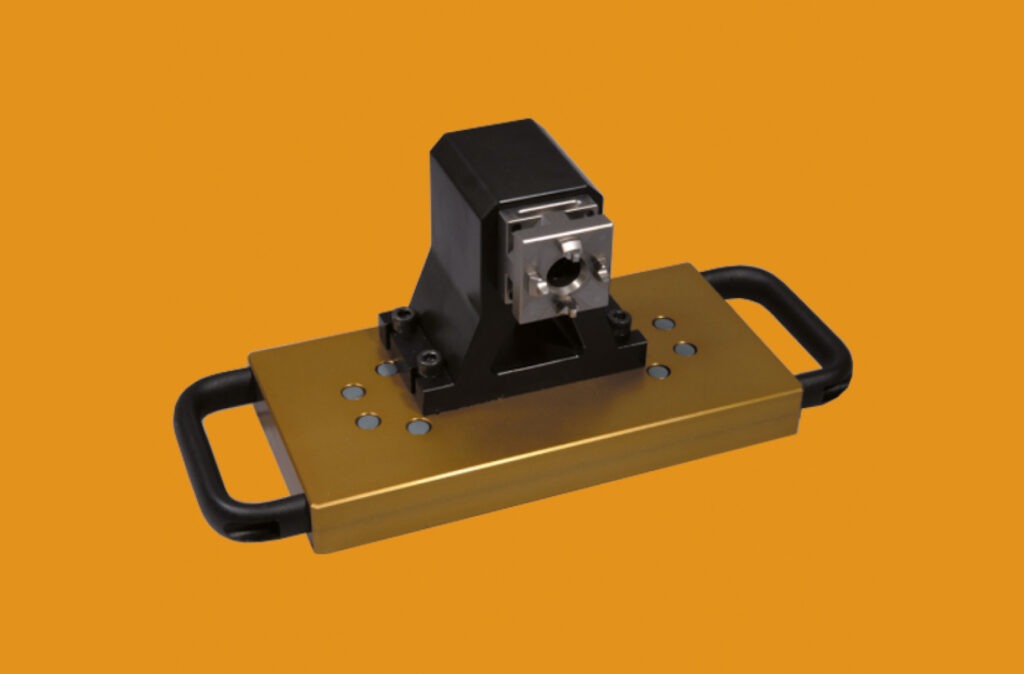
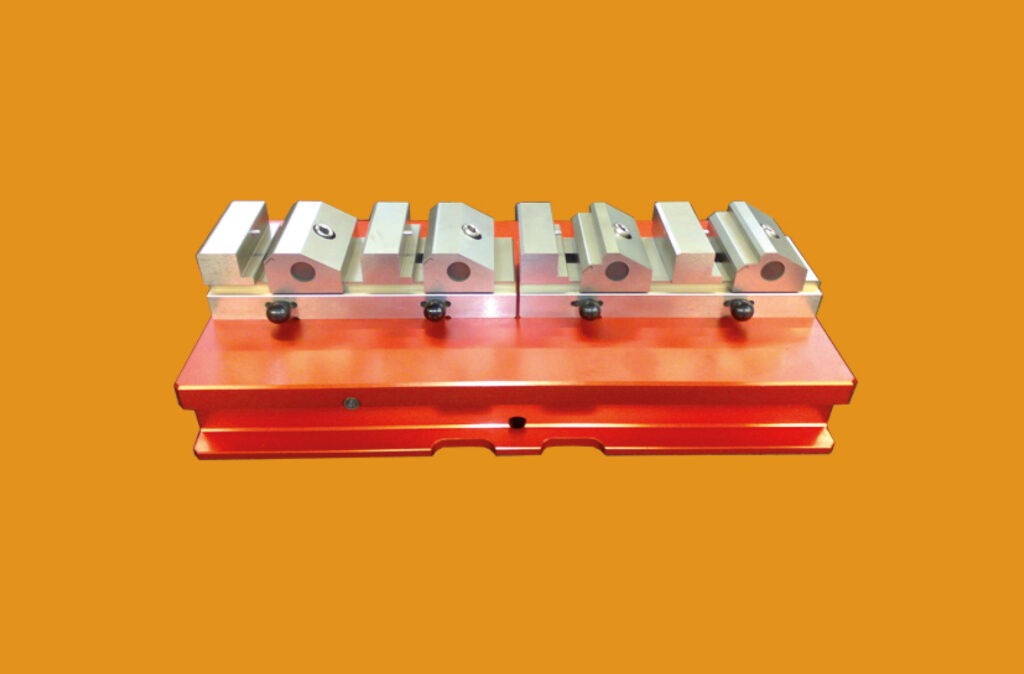
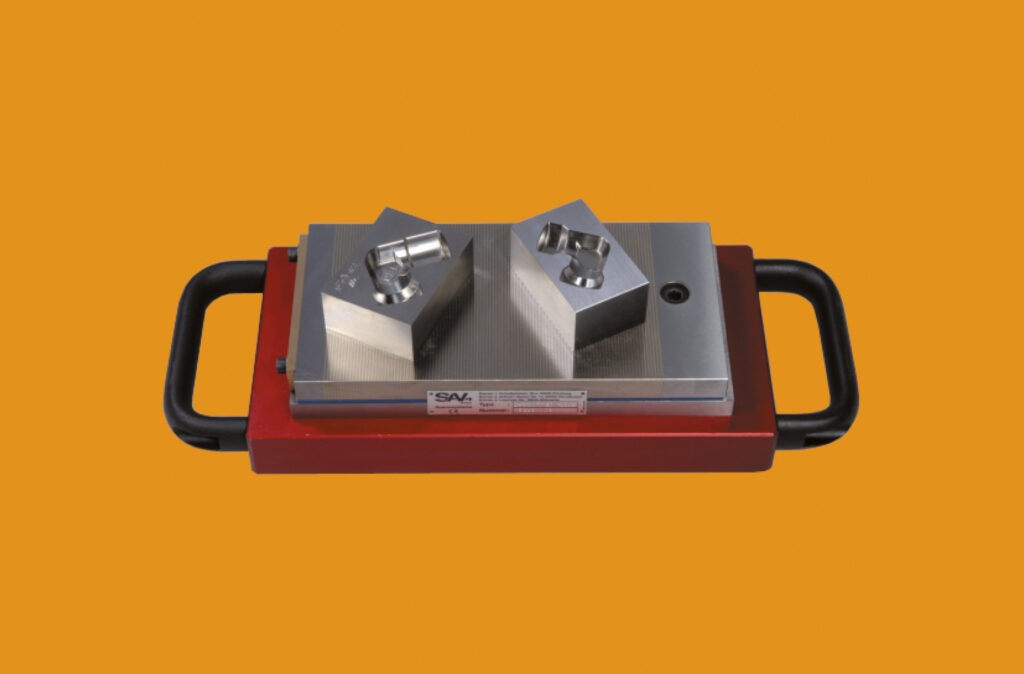
Download Brochure
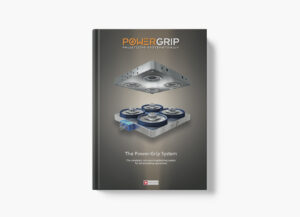